A kind of precision casting sand and preparation method thereof
A technology of precision casting and casting sand, which is applied in the field of precision casting sand and its preparation, which can solve the problems of low yield, high cost, and high energy consumption, and achieve the effects of high yield, strong resistance to crushing, and low energy consumption
- Summary
- Abstract
- Description
- Claims
- Application Information
AI Technical Summary
Problems solved by technology
Method used
Image
Examples
Embodiment 1
[0018] The preparation method of precision casting sand includes the following steps:
[0019] (1) Preparation of mixed powder: a. Grind bauxite, clay, manganese ore, and hematite into 325 mesh fine powder with a pass rate greater than 99% (mass percentage, the same below), and mix according to the following mass percentages: 79% of bauxite, 20% of clay, 0.5% of manganese ore, 0.5% of hematite, mix evenly to obtain mixed powder 1; b. Grind bauxite, clay, manganese ore, and hematite into 325 meshes and pass For fine powder with a rate greater than 99%, mix it in the same proportion as the mixed powder 1, and then grind it to D50<6μm to obtain mixed powder 2;
[0020] (2) Granulation: Put the mixed powder 1 into the granulation pot, rotate at a constant speed and spray (water mist, the same below) to granulate, and select the qualified particles after screening according to the production requirements {according to the sintering shrinkage rate In the case, it should be slightly larg...
Embodiment 2
[0024] The preparation method of precision casting sand includes the following steps:
[0025] (1) Preparation of mixed powder: a. Crush bauxite, clay, manganese ore, and hematite into pieces smaller than 10mm, and mix them according to the following mass percentages: bauxite 95%, clay 3%, manganese ore 1%, hematite 1%, after mixing, grind into 325 mesh fine powder with a pass rate of more than 99% to obtain mixed powder 1; b. Crush bauxite, clay, manganese ore, and hematite into less than 10mm The broken pieces of powder are mixed in the same proportion as the mixed powder 1, and then ground until the 325 mesh pass rate is greater than 99% and the D50 is less than 6 microns to obtain mixed powder 2;
[0026] (2) Granulation: Put the mixed powder 1 into the granulation pot, rotate at a constant speed and granulate under the action of spraying. According to the production requirements, put the qualified particles after screening into the granulation pot and rotate at a constant spee...
Embodiment 3
[0030] The preparation method of precision casting sand includes the following steps:
[0031] (1) Preparation of mixed powder: a. Grind bauxite, clay, manganese ore, and hematite into 325 mesh fine powder with a pass rate of more than 99%, and mix it according to the following mass percentages: bauxite 88%, clay 6.8%, manganese ore 5%, hematite 0.2%, mixed evenly to obtain mixed powder 1; b. Crush bauxite, clay, manganese ore, and hematite into pieces smaller than 10mm, and press the mixed powder 1 After the same proportion of ingredients, grind until the 325 mesh pass rate is greater than 99% and D50<6 microns, to obtain mixed powder 2;
[0032] (2) Granulation: Put the mixed powder 1 into the granulation pot, rotate at a constant speed and granulate under the action of spraying. According to the production requirements, put the qualified particles after screening into the granulation pot and rotate at a constant speed. Add mixed powder 2 for the first time under the action of s...
PUM
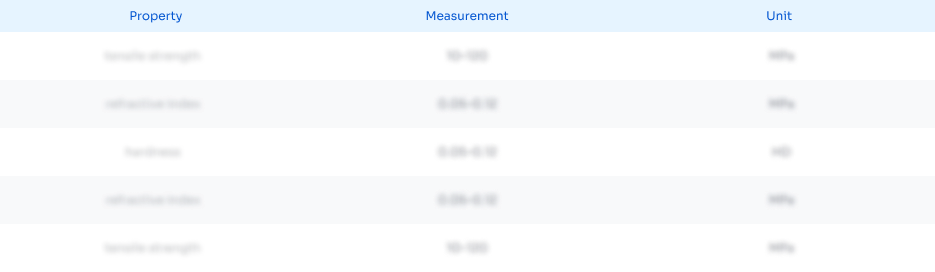
Abstract
Description
Claims
Application Information

- R&D
- Intellectual Property
- Life Sciences
- Materials
- Tech Scout
- Unparalleled Data Quality
- Higher Quality Content
- 60% Fewer Hallucinations
Browse by: Latest US Patents, China's latest patents, Technical Efficacy Thesaurus, Application Domain, Technology Topic, Popular Technical Reports.
© 2025 PatSnap. All rights reserved.Legal|Privacy policy|Modern Slavery Act Transparency Statement|Sitemap|About US| Contact US: help@patsnap.com