Thermally driven mems micromirror and 1×n thermally driven mems micromirror array
A micromirror array, thermally driven technology, applied in microstructure technology, microstructure devices, instruments, etc., can solve the problems of low voltage drive, high mirror filling rate, reduced mirror filling rate, etc., to achieve easy rotation and control, high Mirror fill rate, the effect of reducing thermal crosstalk
- Summary
- Abstract
- Description
- Claims
- Application Information
AI Technical Summary
Problems solved by technology
Method used
Image
Examples
Embodiment Construction
[0024] Embodiments of the present invention will be described below in conjunction with the accompanying drawings.
[0025] Such as figure 1 As shown, the present invention has designed a thermally driven MEMS micromirror, including a mirror surface 1, an electrothermally driven arm 2, and a micromirror frame 3. The mirror surface 1 is respectively arranged with several electrothermally driven arms 2 on the same side, and the said mirror surface 1 is arranged on the same side. Several electrothermal drive arms 2 on the same side of the mirror surface 1 are respectively connected to the micromirror frame 3, so that the two ends of the drive arm 2 are connected to the micromirror frame 3 and the mirror surface 1 respectively, so that the micromirror frame 3 is arranged in pairs on the mirror surface 1 The opposite sides of the micromirror are rotated by applying bias voltages V1, V2, V3, and V4 to each electrothermal driving arm 2 respectively. In practice, the number of electr...
PUM
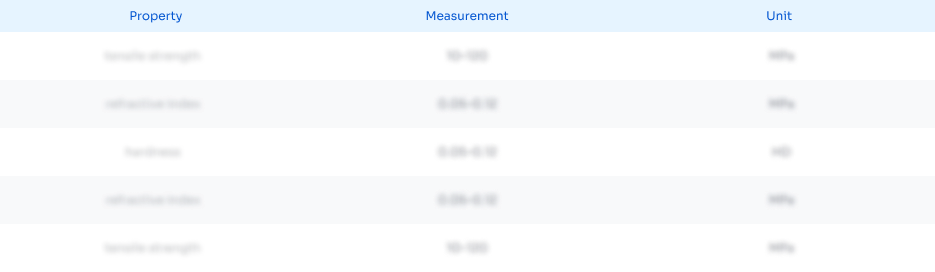
Abstract
Description
Claims
Application Information

- R&D
- Intellectual Property
- Life Sciences
- Materials
- Tech Scout
- Unparalleled Data Quality
- Higher Quality Content
- 60% Fewer Hallucinations
Browse by: Latest US Patents, China's latest patents, Technical Efficacy Thesaurus, Application Domain, Technology Topic, Popular Technical Reports.
© 2025 PatSnap. All rights reserved.Legal|Privacy policy|Modern Slavery Act Transparency Statement|Sitemap|About US| Contact US: help@patsnap.com