Variable structure spherical robot capable of crossing obstacle
A spherical robot, variable structure technology, applied in motor vehicles, transportation and packaging, etc., can solve the problems of small driving torque, stuck in a certain position, loss of movement ability, etc., and achieve the effect of high energy utilization efficiency
- Summary
- Abstract
- Description
- Claims
- Application Information
AI Technical Summary
Problems solved by technology
Method used
Image
Examples
Embodiment 1
[0029] Such as figure 1 , figure 2 , image 3 , Figure 4 , Figure 5 , Image 6 , Figure 7 , Figure 8 As shown, the variable structure spherical robot capable of overcoming obstacles includes a spherical shell O, a counterweight horizontal offset module I, a rolling motion drive module II, a flywheel drive module III and a flywheel brake module IV; The axis of movement of the module is collinear with the axis of rolling motion of the spherical shell 0; the horizontal displacement module I of the counterweight is located in the left cavity of the spherical shell 0 and is connected with the left wall 0-1 of the spherical shell 0; the rolling The motion driving module II is located in the right cavity of the spherical housing 0 and is connected to the right side wall 0-2 of the spherical housing 0; the flywheel driving module III runs through the left side wall 0-1 of the spherical housing 0 and is connected to the left side wall 0-2 The walls 0-1 are connected; th...
Embodiment 2
[0031] This embodiment is basically the same as Embodiment 1, and the special features are as follows:
[0032] Such as figure 1 , figure 2 As shown, the above-mentioned counterweight horizontal offset module I includes a counterweight driving arm 1-1, a first servo motor 1-2, a second servo motor 1-3, a first bearing 1-4, and a feather key 1 -5, counterweight shaft 1-6, second bearing 1-7, counterweight 1-8; described counterweight shaft 1-6 is rotationally connected with spherical shell 0 through first bearing 1-4 , so that the counterweight shaft 1-6 and the spherical shell 0 can rotate axially relative to each other but cannot move axially relative to each other; the sliding key 1-5 is horizontally fixed on the counterweight shaft 1-6; the counterweight 1-8 is socketed On the counterweight shaft 1-6 and the feather key 1-5, the mobile pair is formed; the counterweight driving arm 1-1 is hinged to the counterweight 1-8 through the second bearing 1-7, so that the coun...
PUM
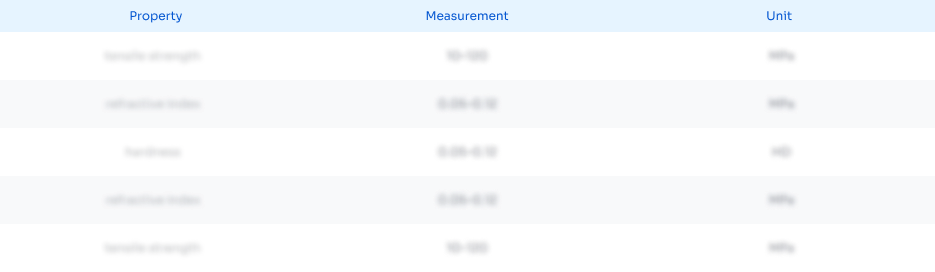
Abstract
Description
Claims
Application Information

- R&D
- Intellectual Property
- Life Sciences
- Materials
- Tech Scout
- Unparalleled Data Quality
- Higher Quality Content
- 60% Fewer Hallucinations
Browse by: Latest US Patents, China's latest patents, Technical Efficacy Thesaurus, Application Domain, Technology Topic, Popular Technical Reports.
© 2025 PatSnap. All rights reserved.Legal|Privacy policy|Modern Slavery Act Transparency Statement|Sitemap|About US| Contact US: help@patsnap.com