Asymmetric Variable Acceleration Planning Method Based on Time Domain Optimal Distribution of Primary Frequency Energy
A technology of optimal distribution and variable acceleration, applied in design optimization/simulation, image data processing, special data processing applications, etc.
- Summary
- Abstract
- Description
- Claims
- Application Information
AI Technical Summary
Problems solved by technology
Method used
Image
Examples
Embodiment example
[0092] The pendulum-type welding head mechanism of the high-speed die-bonding machine needs to move from the crystal-taking position to the die-bonding position at high speed, and must ensure the positioning accuracy of ±1μm, requiring the shortest positioning time. Optimized according to the symmetrical S-shaped acceleration curve, the shortest positioning time obtained is 23.33ms (the driving time is 17.90ms, the maximum residual amplitude is 2.14μm, and the inertial energy decay time is 5.43ms). Through the asymmetric variable acceleration planning proposed in this project, further optimization is carried out. The optimization process is shown in Table 1. Under the same positioning accuracy of ±1μm, the positioning time is 16.36ms (the driving time is 12.90ms, and the maximum residual amplitude is 1.03μm. The decay time of inertial energy is 3.46ms), which is 30% shorter than before (the decay time of inertial energy is reduced by 36%).
[0093] Table 1 Optimization process...
PUM
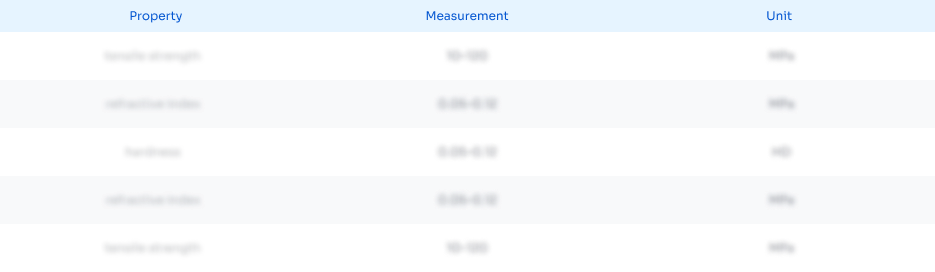
Abstract
Description
Claims
Application Information

- R&D
- Intellectual Property
- Life Sciences
- Materials
- Tech Scout
- Unparalleled Data Quality
- Higher Quality Content
- 60% Fewer Hallucinations
Browse by: Latest US Patents, China's latest patents, Technical Efficacy Thesaurus, Application Domain, Technology Topic, Popular Technical Reports.
© 2025 PatSnap. All rights reserved.Legal|Privacy policy|Modern Slavery Act Transparency Statement|Sitemap|About US| Contact US: help@patsnap.com