A horizontal ultrasonic paper thickness measuring device
An ultrasonic and thickness measuring technology, applied in measuring devices, using ultrasonic/sonic/infrasonic waves, instruments, etc., can solve the problems of reducing the service life of the paper shaft, affecting the normal operation of the equipment, and affecting the measurement accuracy, so as to improve the accuracy and disassemble. Simple and time-saving installation, the effect of high ultrasonic frequency
- Summary
- Abstract
- Description
- Claims
- Application Information
AI Technical Summary
Problems solved by technology
Method used
Image
Examples
Embodiment Construction
[0023] The present invention will be described below in conjunction with specific examples and accompanying drawings.
[0024] The horizontal ultrasonic paper thickness measuring device (thickness measuring device for short) of the present invention comprises a left measuring part and a right measuring part. The measuring part on the left side includes tank body 1, left ultrasonic probe 2, right ultrasonic probe 3, ventilation tube 5, piston 6, right cylindrical tube 7, left cylindrical tube 8, connecting pin 9, upper electromagnet 10, lower electromagnet 11 , Locking pin 12, fixed pin 13, measuring end face 14, spring 15, casing 16, winding paper shaft 17, bracket 18, bearing seat 19, bottom plate 20. The composition of the right measuring part is the same as that of the left measuring part.
[0025] In the left measurement part, the left ultrasonic probe 2 is connected with the bottom of the tank body 1 . The right ultrasonic probe 3 is connected with the left end of the p...
PUM
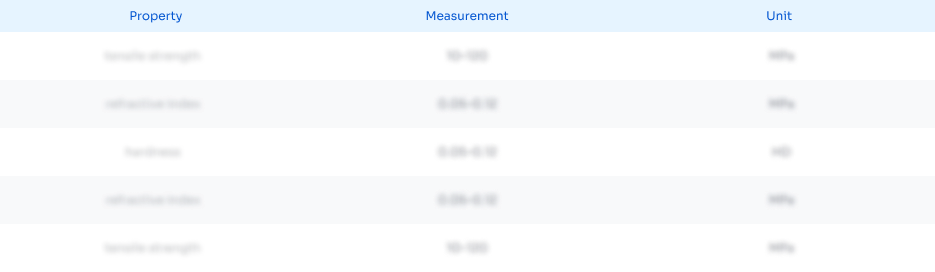
Abstract
Description
Claims
Application Information

- R&D
- Intellectual Property
- Life Sciences
- Materials
- Tech Scout
- Unparalleled Data Quality
- Higher Quality Content
- 60% Fewer Hallucinations
Browse by: Latest US Patents, China's latest patents, Technical Efficacy Thesaurus, Application Domain, Technology Topic, Popular Technical Reports.
© 2025 PatSnap. All rights reserved.Legal|Privacy policy|Modern Slavery Act Transparency Statement|Sitemap|About US| Contact US: help@patsnap.com