Continuous concentration purification method for desulfurization by-product magnesium sulfate solution
A desulfurization by-product, magnesium sulfate technology, applied in the direction of magnesium sulfate, chemical instruments and methods, separation methods, etc., can solve the problems of long time, secondary pollution, high investment and operation costs, etc., to achieve increased oxidation speed and conversion rate, Reduce the cost of desulfurization and realize the effect of resource utilization
- Summary
- Abstract
- Description
- Claims
- Application Information
AI Technical Summary
Problems solved by technology
Method used
Image
Examples
Embodiment 1
[0032] Flue gas condition: 170000Nm 3 / h, SO 2 Concentration 1200mg / Nm 3 , temperature 150°C. The concentration of magnesium oxide slurry is 10%, and the volume is 87m 3 .
[0033] The flue gas enters the desulfurization tower (the desulfurization tower is a spray tower), and the absorption liquid is sprayed into the tower from the upper part. Catalyst is added to the absorption liquid, and the flow rate of the absorption liquid is 1500t / h. SO in the flue gas exiting the top of the tower 2 The content is 30mg / Nm 3 , The desulfurization rate is 97.5%. After desulfurization, the flue gas enters the chimney from the top of the tower after being demistered by the demister. After 20h, a solution containing 25% magnesium sulfate was obtained. Take out a part of the absorption liquid, after evaporation, concentration and cooling, magnesium sulfate crystallizes out, and after filtration and drying, magnesium sulfate heptahydrate is obtained, with a content of 99.5%.
[0034]
Embodiment 2
[0036] Flue gas condition: 6500Nm 3 / h, SO 2 Concentration 2286mg / Nm 3 ), the temperature is 140°C. The concentration of magnesium oxide slurry is 10%, the volume is 3.0m 3
[0037] The flue gas enters the desulfurization tower (the desulfurization tower is a spray tower). The absorption liquid is sprayed into the tower from the upper part, and the catalyst is added to the absorption liquid. The flow rate of the absorption liquid is 10t / h. SO in the flue gas exiting the top of the tower 2 The content is 40mg / Nm 3 , the desulfurization rate is 98.2%. After desulfurization, the flue gas enters the chimney from the top of the tower after being demistered by the demister. After 47h, a solution containing 23.6% magnesium sulfate was obtained. Take out a part of the absorption liquid, after evaporation, concentration and cooling, magnesium sulfate crystallizes out, and after filtration and drying, magnesium sulfate heptahydrate is obtained.
[0038]
Embodiment 3
[0040] Flue gas condition: 45000Nm 3 / h, SO 2 Concentration 914mg / Nm 3 , temperature 160°C. The concentration of magnesium oxide slurry is 15%, the volume is 7m 3 .
[0041] The flue gas enters the desulfurization tower (the desulfurization tower is a spray tower), and the absorption liquid is sprayed into the tower from the upper part. Catalyst is added to the absorption liquid, and the flow rate of the absorption liquid is 30t / h. SO in the flue gas exiting the top of the tower 2 The content is 20mg / Nm 3 , the desulfurization rate is 97.8%. After desulfurization, the flue gas enters the chimney from the top of the tower after being demistered by the demister. After 21 hours, a solution containing 22.6% magnesium sulfate was obtained. Take out a part of the absorption liquid, and undergo conventional crystallization separation to obtain magnesium sulfate heptahydrate with a content of 99.4%.
PUM
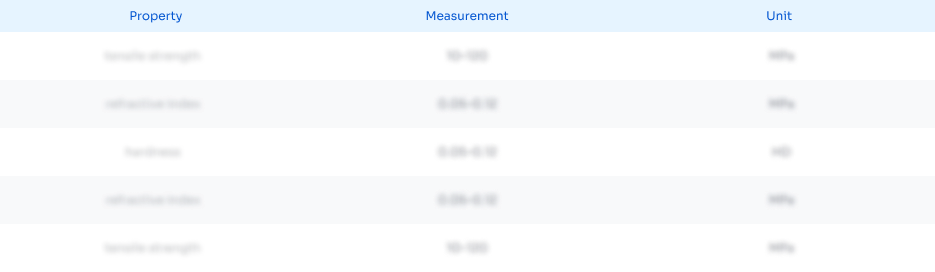
Abstract
Description
Claims
Application Information

- Generate Ideas
- Intellectual Property
- Life Sciences
- Materials
- Tech Scout
- Unparalleled Data Quality
- Higher Quality Content
- 60% Fewer Hallucinations
Browse by: Latest US Patents, China's latest patents, Technical Efficacy Thesaurus, Application Domain, Technology Topic, Popular Technical Reports.
© 2025 PatSnap. All rights reserved.Legal|Privacy policy|Modern Slavery Act Transparency Statement|Sitemap|About US| Contact US: help@patsnap.com