A production process of high-density polyethylene winding wall carat tube
A high-density polyethylene and wall-carat tube technology, which is applied to tubular articles, other household appliances, household appliances, etc., can solve the problems of danger to operators, great physical harm, and low heating efficiency, and achieves simple and convenient operation. The effect of resistance to external pressure and high heating efficiency
- Summary
- Abstract
- Description
- Claims
- Application Information
AI Technical Summary
Problems solved by technology
Method used
Image
Examples
Embodiment 1
[0033] First, the equipment is preheated for more than 3 hours, after the temperature reaches the set value. Start mixing, mix according to the ratio of 100 parts of HDPE resin, 3 parts of color masterbatch, and 15 parts of short-wave fiber masterbatch, and the mixing time is 5 minutes. The material is sucked into the hopper of the extruder by the vacuum suction machine. After the extruder is turned on, the servo motor (5) is turned on to make the heating plate (9) close to the mold drum (3). After heating to 100°C, winding is carried out, first winding the socket position, then winding the straight section, and finally winding the forming socket. Hoist the mold drum (3) onto the turning table by driving, and cut the socket and socket positions at the same time. After reaching a certain size requirement, use the cooling fan (2) for air cooling. After the pipe is cooled to 60°C, hoist the drum to the The demoulding machine is used for demoulding. After the completion, the sock...
Embodiment 2
[0035] First, the equipment is preheated for more than 3 hours, after the temperature reaches the set value. Start mixing, mix according to the ratio of 100 parts of HDPE resin, 3 parts of color masterbatch, and 20 parts of short-wave fiber masterbatch, and the mixing time is 5 minutes. The material is sucked into the hopper of the extruder by the vacuum suction machine. After the extruder is turned on, the servo motor (5) is turned on to make the heating plate (9) close to the mold drum (3). After heating to 130°C, winding is carried out. First, the position of the socket is wound, then the straight section is wound, and finally the socket is formed. Hoist the mold drum (3) onto the turning table by driving, and cut the socket and socket positions at the same time. After reaching a certain size requirement, use the cooling fan (2) for air cooling. After the pipe is cooled to 60°C, hoist the drum to the The demoulding machine is used for demoulding. After the completion, the ...
Embodiment 3
[0037] First, the equipment is preheated for more than 3 hours, after the temperature reaches the set value. Start mixing, mix according to the ratio of 100 parts of HDPE resin, 3 parts of color masterbatch, and 30 parts of short-wave fiber masterbatch, and the mixing time is 5 minutes. The material is sucked into the hopper of the extruder by the vacuum suction machine. After the extruder is turned on, the servo motor (5) is turned on to make the heating plate (9) close to the mold drum (3). After heating to 150°C, winding is carried out. First, the position of the socket is wound, then the straight section is wound, and finally the socket is formed. Hoist the mold drum (3) onto the turning table by driving, and cut the socket and socket positions at the same time. After reaching a certain size requirement, use the cooling fan (2) for air cooling. After the pipe is cooled to 60°C, hoist the drum to the The demoulding machine is used for demoulding. After the completion, the ...
PUM
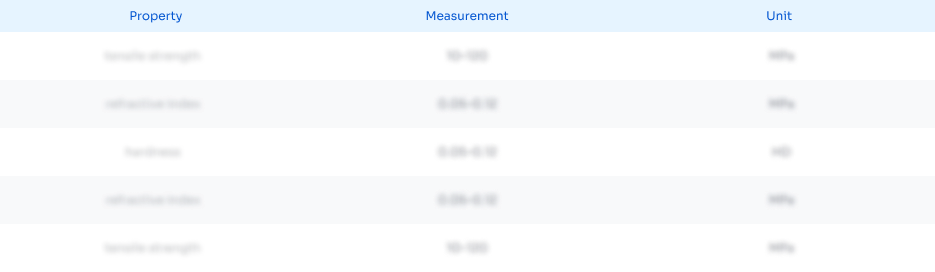
Abstract
Description
Claims
Application Information

- Generate Ideas
- Intellectual Property
- Life Sciences
- Materials
- Tech Scout
- Unparalleled Data Quality
- Higher Quality Content
- 60% Fewer Hallucinations
Browse by: Latest US Patents, China's latest patents, Technical Efficacy Thesaurus, Application Domain, Technology Topic, Popular Technical Reports.
© 2025 PatSnap. All rights reserved.Legal|Privacy policy|Modern Slavery Act Transparency Statement|Sitemap|About US| Contact US: help@patsnap.com