Non-contact active control method for vibration of micro thrust measurement system
A measurement system, non-contact technology, applied in the direction of using feedback control, etc., can solve the problems of measurement error, small vibration damping effect is not obvious, etc., and achieve the effect of high control accuracy
- Summary
- Abstract
- Description
- Claims
- Application Information
AI Technical Summary
Problems solved by technology
Method used
Image
Examples
Embodiment Construction
[0020] The invention uses the Ampere force between the local magnetic field and the current-carrying coil as the control force, uses the sensor to measure the angular displacement of the swing arm or beam, and controls the vibration of the swing arm or beam through an automatic control method to stabilize it at a balanced position .
[0021] attached figure 1 The schematic diagram of the vibration control system of the torsion beam is shown, and the vibration control steps are as follows:
[0022] 1. Install the force coil 3 on the torsion beam 1, the positions of the force coil 3 and the local uniform magnetic field 4 are as follows figure 1 shown. A part of the force coil 3 (0.15mm enamelled copper wire, 20 turns) passes through the local uniform magnetic field 4, and the energized force coil will be subjected to an upward or downward ampere force along the paper surface under the action of the magnetic field. Assuming that the length of the local uniform magnetic field 4...
PUM
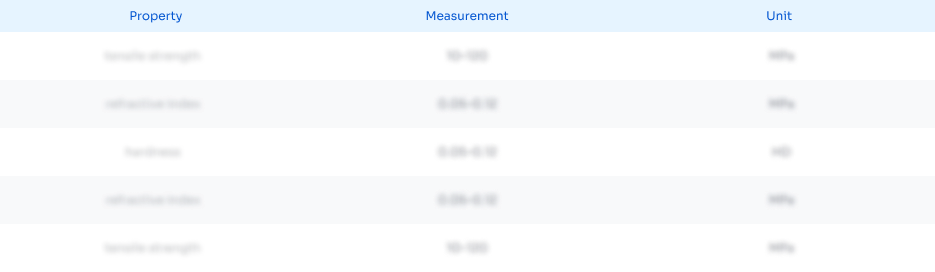
Abstract
Description
Claims
Application Information

- R&D
- Intellectual Property
- Life Sciences
- Materials
- Tech Scout
- Unparalleled Data Quality
- Higher Quality Content
- 60% Fewer Hallucinations
Browse by: Latest US Patents, China's latest patents, Technical Efficacy Thesaurus, Application Domain, Technology Topic, Popular Technical Reports.
© 2025 PatSnap. All rights reserved.Legal|Privacy policy|Modern Slavery Act Transparency Statement|Sitemap|About US| Contact US: help@patsnap.com