Multi-dimensional force sensor calibration device with controllable poses
A multi-dimensional force sensor and calibration device technology, which is applied in the direction of measuring devices, instruments, force/torque/power measuring instrument calibration/testing, etc., can solve the problems of unsuitable sensor calibration work, long calibration time, unfavorable sensor promotion, etc. problems, to achieve the effect of high rigidity, large bearing capacity and small inertia
- Summary
- Abstract
- Description
- Claims
- Application Information
AI Technical Summary
Problems solved by technology
Method used
Image
Examples
Embodiment Construction
[0024] The present invention will be further described below with examples in conjunction with the accompanying drawings.
[0025] to combine figure 1 , the present invention mainly is made up of fixed platform mechanism 1, drive mechanism 2, connecting rod mechanism 3, universal hinge mechanism 4, moving platform mechanism 5. The present invention adopts a typical Stewart type parallel structure. The mechanism has two platforms, upper and lower, which are connected sequentially through six connecting rod mechanisms driven by servo motors. The upper ends of the six connecting rod mechanisms are hinged with the moving platform through universal hinges, while the lower ends are hinged with the fixed platform, forming six degrees of freedom. parallel mechanism. The six linkage mechanisms are divided into three groups, and two adjacent linkage mechanisms form a group, which is arranged in a figure of eight. The six positions hinged with the fixed platform are distributed on the...
PUM
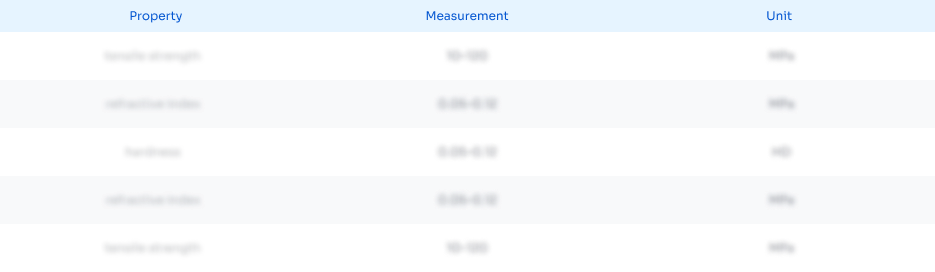
Abstract
Description
Claims
Application Information

- R&D Engineer
- R&D Manager
- IP Professional
- Industry Leading Data Capabilities
- Powerful AI technology
- Patent DNA Extraction
Browse by: Latest US Patents, China's latest patents, Technical Efficacy Thesaurus, Application Domain, Technology Topic, Popular Technical Reports.
© 2024 PatSnap. All rights reserved.Legal|Privacy policy|Modern Slavery Act Transparency Statement|Sitemap|About US| Contact US: help@patsnap.com