Under-actuated ingenious multifunctional space robot hand claw
A space robot, multi-functional technology, applied in manipulators, program-controlled manipulators, chucks, etc., can solve the problems of small grasping force, inflexibility, single function, etc., achieve long working life, improve grasping or clamping accuracy, Control simple effects
- Summary
- Abstract
- Description
- Claims
- Application Information
AI Technical Summary
Problems solved by technology
Method used
Image
Examples
Embodiment Construction
[0030] Further description below in conjunction with accompanying drawings.
[0031] 1) see figure 1 , set the cylindrical front end sleeve 5 and the tail end sleeve 4 to form a static body by connecting and fastening the sleeve fastener 5.1, and the fastener adopts pins or screws to limit the movement and rotation of the tail end sleeve 4. Drive motor 9 supports are fixed with front end sleeve. The driving motor can be a stepper motor. The driving motor is fixed in the mechanical arm 10 of the space robot. In the inner cavity of the front sleeve, the ball screw installed is a precision ball screw. Its ball screw rod 6 is composed as follows: ① see figure 1 , a screw mandrel 6.1 is provided, the front end is connected to the rotating shaft of the drive motor 9 through a coupling 8, and the screw mandrel is provided with a screw mandrel support 7 fixed to the front end sleeve to support the screw mandrel. ② see figure 2 , Screw mandrel 6.1 overcoat has ball nut seat 6.2:...
PUM
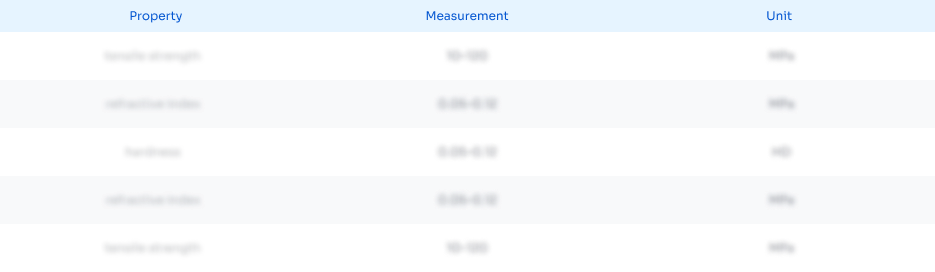
Abstract
Description
Claims
Application Information

- R&D Engineer
- R&D Manager
- IP Professional
- Industry Leading Data Capabilities
- Powerful AI technology
- Patent DNA Extraction
Browse by: Latest US Patents, China's latest patents, Technical Efficacy Thesaurus, Application Domain, Technology Topic, Popular Technical Reports.
© 2024 PatSnap. All rights reserved.Legal|Privacy policy|Modern Slavery Act Transparency Statement|Sitemap|About US| Contact US: help@patsnap.com