Diesel Engine Cylinder Head Casting Process
A casting process and diesel engine technology, which is applied in manufacturing tools, casting molding equipment, casting molds, etc., can solve problems such as cavities, shrinkage cavities, affecting the quality of cylinder head casting, engine performance, and easy water leakage in cooling water chambers, so as to reduce water leakage The effect of reducing the shrinkage cavity of castings and facilitating operation
- Summary
- Abstract
- Description
- Claims
- Application Information
AI Technical Summary
Problems solved by technology
Method used
Image
Examples
Embodiment Construction
[0024] A specific embodiment of the present invention will be described in detail below in conjunction with the accompanying drawings, but it should be understood that the protection scope of the present invention is not limited by the specific embodiment. It should be understood that the "upper", "lower", "left", "right", "front" and "reverse" mentioned in the following embodiments of the present invention are all based on the directions shown in the figures, These words used to limit the direction are only for convenience of description, and do not mean to limit the specific technical solution of the present invention.
[0025] In the diesel engine cylinder head casting process of the present invention, during the molding process of the chassis core, a fully enclosed cooling jacket is provided at the place where the sand core passes through the nail hole, so that the molten iron passing through the nail hole can be rapidly cooled and simultaneously cooled and solidified, so a...
PUM
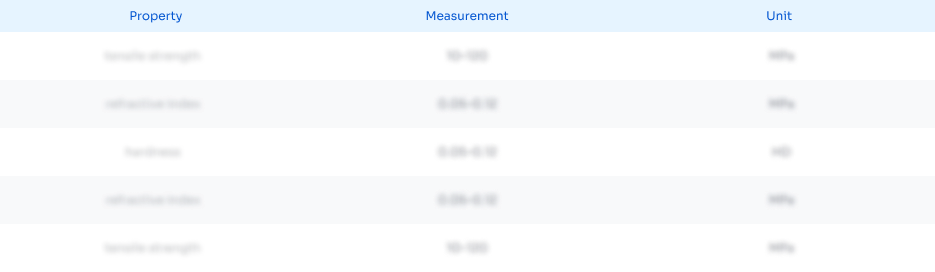
Abstract
Description
Claims
Application Information

- R&D
- Intellectual Property
- Life Sciences
- Materials
- Tech Scout
- Unparalleled Data Quality
- Higher Quality Content
- 60% Fewer Hallucinations
Browse by: Latest US Patents, China's latest patents, Technical Efficacy Thesaurus, Application Domain, Technology Topic, Popular Technical Reports.
© 2025 PatSnap. All rights reserved.Legal|Privacy policy|Modern Slavery Act Transparency Statement|Sitemap|About US| Contact US: help@patsnap.com