Micron-scale inverse magnetostrictive driver and method of use
A technology of inverse magnetostriction and drive, applied in the direction of piezoelectric effect/electrostriction or magnetostriction motor, generator/motor, electrical components, etc., can solve the problem of current heat loss and magnetic permeability of magnetostrictive materials Low energy consumption, high energy consumption and other issues, to achieve the effect of stable work and suitable for high-precision positioning
- Summary
- Abstract
- Description
- Claims
- Application Information
AI Technical Summary
Problems solved by technology
Method used
Image
Examples
Embodiment 1
[0022] Embodiment 1, figure 1 , image 3 with Image 6 Provided is a micron-scale magnetostrictive actuator and a use method; a micron-scale magnetostrictive actuator includes a driver and a mover iron core 6 . The driver includes the end iron-gallium alloy magnetic core 1, the end permanent magnet magnetic core 2, the iron-gallium alloy 3, the magnet 4 (permanent magnet as an example) and the base magnetic core 5; the end iron-gallium alloy magnetic core 1 An iron-gallium alloy 3 is arranged between the base and the base magnetic core 5; a magnet 4 is arranged between the end permanent magnet magnetic core 2 and the base magnetic core 5. The iron-gallium alloy magnetic core 1 at the end, the iron-gallium alloy 3 and the base magnetic core 5 are provided with the mover iron core 6; the magnet 4 is axially magnetized; the magnet 4, the base magnetic core 5, the iron-gallium alloy 3, the end The iron-gallium alloy magnetic core 1 at the end and the permanent magnet magnetic c...
Embodiment 2
[0035] Embodiment 2, figure 2 , Figure 4 with Figure 5 A micron-scale magnetostrictive actuator is given, the end permanent magnet magnetic core 2 and the magnet 4 are set on the end iron-gallium alloy magnetic core 1 and the iron-gallium alloy 3; the permanent magnet magnetic core 2 and the magnet 4 Put on the mover iron core 6. The magnet 4 is axially magnetized, and through axial magnetization, a magnetic circuit I7 is formed on the base magnetic core 5, the iron-gallium alloy 3 and the end iron-gallium alloy magnetic core 1; the base magnetic core 5, the mover iron core 6 and the magnetically permeable core 2 form a magnetic circuit II8.
[0036] In actual use, a plurality of drivers are connected in series and used in conjunction with a single mover core 6 .
[0037] In actual use, the steps and principles of use are exactly the same as those in Embodiment 1.
[0038] When selecting the magnetostrictive material mentioned above, you can use Terfenol (the earliest ap...
PUM
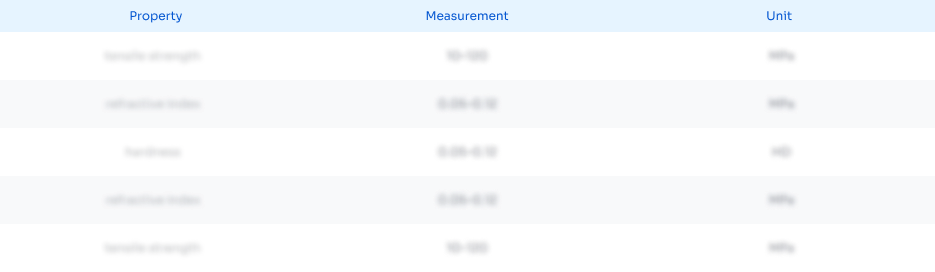
Abstract
Description
Claims
Application Information

- R&D
- Intellectual Property
- Life Sciences
- Materials
- Tech Scout
- Unparalleled Data Quality
- Higher Quality Content
- 60% Fewer Hallucinations
Browse by: Latest US Patents, China's latest patents, Technical Efficacy Thesaurus, Application Domain, Technology Topic, Popular Technical Reports.
© 2025 PatSnap. All rights reserved.Legal|Privacy policy|Modern Slavery Act Transparency Statement|Sitemap|About US| Contact US: help@patsnap.com