Beam-end loaded plane frame joint pseudo-static test loading device
A loading device and quasi-static technology, applied in the seismic field of building structures, can solve problems such as instrument damage and test deviation, and achieve the effects of high experimental accuracy, easy control, and simple structure of the loading device
- Summary
- Abstract
- Description
- Claims
- Application Information
AI Technical Summary
Problems solved by technology
Method used
Image
Examples
Embodiment Construction
[0017] combine figure 1 and figure 2 The invention is described. The loading device for the pseudo-static test of the plane frame node loaded at the beam end of the present invention mainly includes a hinge column shoe 3, a column cap 2, a loading spherical hinge 5, a loading system and a data acquisition system. Hinge column shoe 3 is used to cover the column foot of component 1, and column cap 2 is used to cover the column head of component. Two sets of loading spherical hinges 5 are respectively installed on the left beam end and right beam end of the component. The loading system is connected with the loading spherical hinge, so that The components are loaded, and the data acquisition system is used to collect relevant mechanical information of the test components.
[0018] Such as image 3 and Figure 4 As shown, the loaded ball joint includes a ball core 6, a bottom plate 7, a lower top plate 8, an upper top plate 9, and a screw 10; the bottom plate is provided with...
PUM
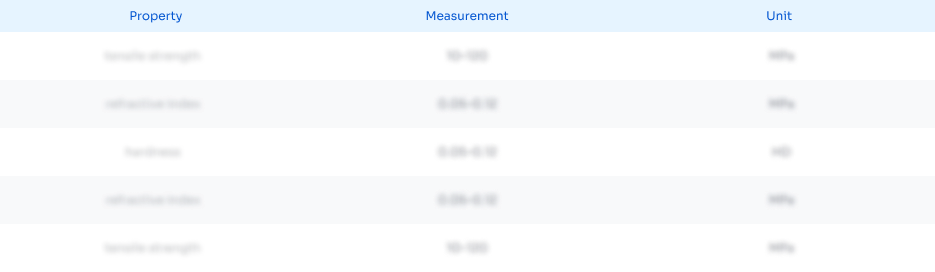
Abstract
Description
Claims
Application Information

- Generate Ideas
- Intellectual Property
- Life Sciences
- Materials
- Tech Scout
- Unparalleled Data Quality
- Higher Quality Content
- 60% Fewer Hallucinations
Browse by: Latest US Patents, China's latest patents, Technical Efficacy Thesaurus, Application Domain, Technology Topic, Popular Technical Reports.
© 2025 PatSnap. All rights reserved.Legal|Privacy policy|Modern Slavery Act Transparency Statement|Sitemap|About US| Contact US: help@patsnap.com