A method and mold with a gap surface fiber tube
A fiber tube and curved surface technology, which is applied in the field of preparation of notched curved surface fiber tubes, can solve the problems of loose fiber material winding, reduce the structural strength of fiber tubes, and low yield, and achieve uniform thickness, improved structural strength, and neat lines Effect
- Summary
- Abstract
- Description
- Claims
- Application Information
AI Technical Summary
Problems solved by technology
Method used
Image
Examples
preparation example Construction
[0016] The invention provides a method for preparing a fiber tube with a notched curved surface, the process of which is as follows figure 1 As shown, it specifically includes the following steps:
[0017] S10. Make a metal inner core according to the shape of the product, and set a clamping device on both sides of the inner core; wind the cut fiber cloth on the metal inner core, and wind the two ends of the fiber cloth on the clamping device ; And tighten the clamping device to make the fiber cloth tight;
[0018] S20, prepare the mould, put the metal inner core wrapped with taut fiber cloth into the mould, close the mold and compress the fiber cloth;
[0019] S30. After clamping the mold, heat and press to form, and cool to form; after the mold is opened, a fiber tube with a curved surface with notches is obtained; the metal inner core is first separated, and the fiber tube is finished to obtain a finished product.
[0020] In the preparation method provided by the present...
Embodiment 1
[0040] Prepare the metal inner core 24 according to the shape of the product, and set the clamping device on the metal core material; cut the fiber cloth 41, wind the cut fiber cloth 41 on the metal inner core 24, and wrap the two ends of the fiber cloth 41 respectively fixed on the clamping device, and the fiber cloth 41 is tightened by the clamping device so that it closely fits with the metal inner core 24 or other fiber cloth; the metal inner core 24 is put into the opened mold, and the upper mold 21 moves down and gradually approaches the metal inner core 24, and the movement of the upper mold 21 drives the first slider 22 and the second slider 26 to move towards the metal inner core 24 until the upper mold 21, the lower mold 26, the first slider 22, the second slider The two sliding parts 26 are in close contact with the metal inner core 24 .
[0041] After the mold is closed, the mold is heated and pressurized to form the fiber cloth 41, wherein the heating temperature ...
Embodiment 2
[0043] Prepare the metal inner core 24 according to the shape of the product, and set the clamping device on the metal core material; cut the fiber cloth 41, wind the cut fiber cloth 41 on the metal inner core 24, and wrap the two ends of the fiber cloth 41 respectively fixed on the clamping device, and the fiber cloth 41 is tightened by the clamping device so that it closely fits with the metal inner core 24 or other fiber cloth; the metal inner core 24 is put into the opened mold, and the upper mold 21 moves down and gradually approaches the metal inner core 24, and the movement of the upper mold 21 drives the first slider 22 and the second slider 26 to move towards the metal inner core 24 until the upper mold 21, the lower mold 26, the first slider 22, the second slider The two sliding parts 26 are in close contact with the metal inner core 24 .
[0044] After the mold is closed, the mold is heated and pressurized to shape the fiber cloth 41, wherein the heating temperature...
PUM
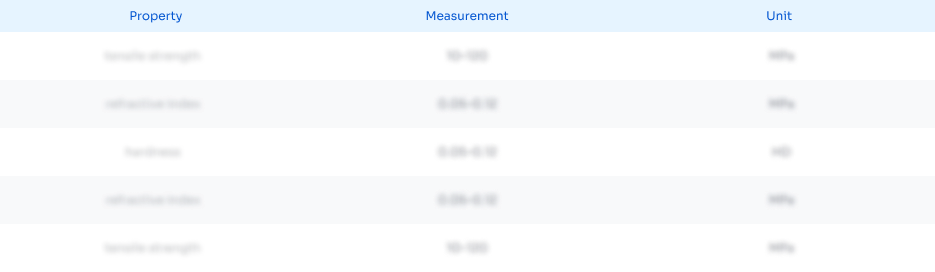
Abstract
Description
Claims
Application Information

- R&D Engineer
- R&D Manager
- IP Professional
- Industry Leading Data Capabilities
- Powerful AI technology
- Patent DNA Extraction
Browse by: Latest US Patents, China's latest patents, Technical Efficacy Thesaurus, Application Domain, Technology Topic, Popular Technical Reports.
© 2024 PatSnap. All rights reserved.Legal|Privacy policy|Modern Slavery Act Transparency Statement|Sitemap|About US| Contact US: help@patsnap.com