Control method and drive device for robot flexible joints
A technology of flexible joints and control methods, which is applied in the field of robotics and can solve problems such as poor control performance
- Summary
- Abstract
- Description
- Claims
- Application Information
AI Technical Summary
Problems solved by technology
Method used
Image
Examples
Embodiment Construction
[0049] Such as figure 2 , 3 As shown, the driving device of the flexible joint of the robot in the embodiment of the present invention includes several flexible joints and a host computer, and each flexible joint includes a spring arranged between the load and the motor reducer, and the two ends of the spring are equipped with absolute The encoder also includes a servo drive that drives the movement of the flexible joints. The upper computer is used to plan the motion of each flexible joint. A function expansion card is also connected between each flexible joint and the upper computer. The function expansion card includes:
[0050] The signal conversion module converts the differential SSI signal output by the absolute encoder into a level SSI signal;
[0051] The SSI communication module converts the level SSI standard signal obtained by the signal conversion module into a digital signal;
[0052] MCU preprocesses the digital signal from the SSI communication module, and c...
PUM
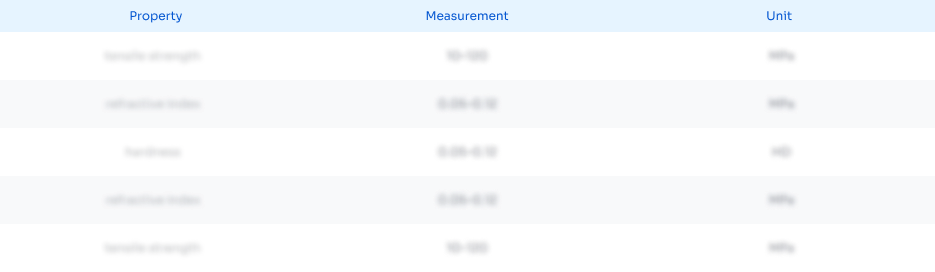
Abstract
Description
Claims
Application Information

- R&D Engineer
- R&D Manager
- IP Professional
- Industry Leading Data Capabilities
- Powerful AI technology
- Patent DNA Extraction
Browse by: Latest US Patents, China's latest patents, Technical Efficacy Thesaurus, Application Domain, Technology Topic, Popular Technical Reports.
© 2024 PatSnap. All rights reserved.Legal|Privacy policy|Modern Slavery Act Transparency Statement|Sitemap|About US| Contact US: help@patsnap.com