Bending mode supersonic vibration auxiliary cutting device for precision or ultra-precision turning
A technology of ultrasonic vibration and cutting devices, applied in auxiliary devices, fluids using vibration, turning equipment, etc., to improve processing efficiency, ensure processing accuracy, and ensure rigidity
- Summary
- Abstract
- Description
- Claims
- Application Information
AI Technical Summary
Problems solved by technology
Method used
Image
Examples
Embodiment Construction
[0038] Below in conjunction with embodiment and accompanying drawing, the present invention will be further described:
[0039] see figure 1 , Figure 1A , Figure 1B As shown, a bending mode ultrasonic vibration assisted cutting device for precision or ultra-precision turning of the present invention, the cutting device includes an ultrasonic vibration unit 2, a housing 1 set on the outer surface of the ultrasonic vibration unit 2 and a top through the front end of the housing 1. The threaded hole 216 and the knife groove 215 are installed on the cutter 3 on the output end of the ultrasonic vibration unit 2 .
[0040] (1) Ultrasonic vibration unit 2
[0041] see Figure 1B As shown, the ultrasonic vibration unit 2 includes a flanged front cover 21, an excitation source 22, a rear cover 23 and fastening screws 24; the structure of the rear cover (23) is a hollow cylinder structure.
[0042] see figure 2 As shown, the flanged front cover 21 is a stepped shaft structure tha...
PUM
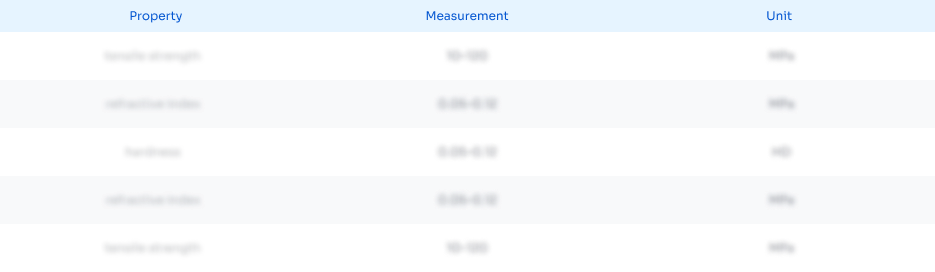
Abstract
Description
Claims
Application Information

- Generate Ideas
- Intellectual Property
- Life Sciences
- Materials
- Tech Scout
- Unparalleled Data Quality
- Higher Quality Content
- 60% Fewer Hallucinations
Browse by: Latest US Patents, China's latest patents, Technical Efficacy Thesaurus, Application Domain, Technology Topic, Popular Technical Reports.
© 2025 PatSnap. All rights reserved.Legal|Privacy policy|Modern Slavery Act Transparency Statement|Sitemap|About US| Contact US: help@patsnap.com