Laminated type PVDF actuator and active and passive hybrid vibration isolator
A hybrid vibration isolator and actuator technology, applied in the direction of shock absorbers, shock absorbers, springs/shock absorbers, etc., can solve the problems of amplifying vibration, large volume of piezoelectric stacks, and no vibration isolation effect in low frequency regions. , to achieve the effect of improving the vibration isolation performance
- Summary
- Abstract
- Description
- Claims
- Application Information
AI Technical Summary
Problems solved by technology
Method used
Image
Examples
Embodiment 1
[0041] This embodiment is a laminated PVDF actuator.
[0042] like figure 1 , figure 2 , image 3 As shown, a stacked PVDF actuator of this embodiment includes a multilayer PVDF piezoelectric film unit, and PET films 12 are pasted on both sides of the multilayer PVDF piezoelectric film unit; the multilayer PVDF piezoelectric film unit Among them, the polarization directions of the two adjacent PVDF piezoelectric films 10 are opposite, and they are bonded through the epoxy resin layer 9; between each layer of PVDF piezoelectric films 10, between PVDF piezoelectric films 10 and PET films Corresponding positions are pasted plain weave conductive adhesive tape 13 respectively. Among them, the multi-layer PVDF piezoelectric films 10 are connected in the manner of "mechanical series connection and electrical parallel connection". The place is bonded with a layer of epoxy resin layer 9, and a layer of epoxy resin layer 11 is used between the PVDF piezoelectric film 10 and t...
Embodiment 2
[0046] This embodiment is an active-passive hybrid vibration isolator based on a laminated PVDF actuator.
[0047] like figure 1 , figure 2 , image 3 As shown, it includes a laminated PVDF actuator 3 connected to an external controlled object 1 on one side, and connected to a base 8 on the other side of the laminated PVDF actuator 3 . The active-passive hybrid vibration isolator also includes a middle connecting piece 5 and a rubber pad 6, wherein the laminated PVDF actuator 3 is arranged between the controlled object 1 and the middle connecting piece 5, and the middle connecting piece 5 passes through the rubber pad. Pad 6 is connected to base 8 .
[0048] like figure 1 , figure 2 As shown, the connection method of each part in this embodiment is that the controlled object 1 and the laminated PVDF actuator 3 are bonded with epoxy resin, and the laminated PVDF actuator 3 and the middle part The connecting piece 5 is bonded with epoxy resin, the middle connecting pie...
PUM
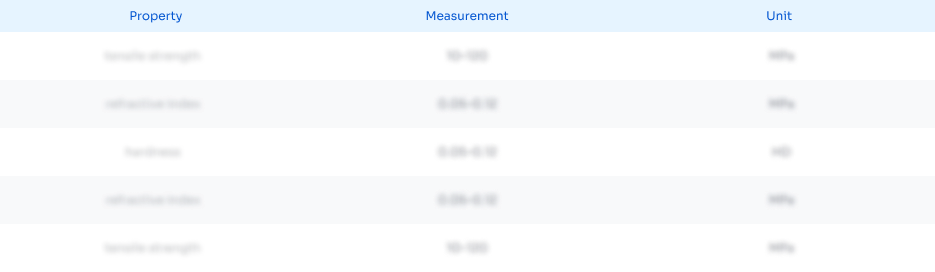
Abstract
Description
Claims
Application Information

- R&D
- Intellectual Property
- Life Sciences
- Materials
- Tech Scout
- Unparalleled Data Quality
- Higher Quality Content
- 60% Fewer Hallucinations
Browse by: Latest US Patents, China's latest patents, Technical Efficacy Thesaurus, Application Domain, Technology Topic, Popular Technical Reports.
© 2025 PatSnap. All rights reserved.Legal|Privacy policy|Modern Slavery Act Transparency Statement|Sitemap|About US| Contact US: help@patsnap.com