Centrifugal pump flow induction noise numerical prediction method
A noise-induced and numerical prediction technology, applied in the direction of electrical digital data processing, special data processing applications, instruments, etc., can solve the problems of not considering the structure of the pump body, and achieve the effect of reducing the number of tests, shortening the research and development cycle, and saving development costs
- Summary
- Abstract
- Description
- Claims
- Application Information
AI Technical Summary
Problems solved by technology
Method used
Image
Examples
Embodiment Construction
[0031] The present invention will be further described below in conjunction with the accompanying drawings and specific embodiments.
[0032] Depend on figure 1 , figure 2 As shown, a numerical prediction method of centrifugal pump flow-induced noise, using the combination of large eddy simulation and acoustic finite element and coupled structural vibration, and in the process of centrifugal pump flow noise calculation, the combination of ACTRAN Aero-Acoustics module and Vibro-Acoustics Solve the design conditions (Q=25m 3 / s), including the following steps:
[0033] Step 1) Perform external characteristic tests on the model pump to obtain the boundary condition data required for numerical calculation: inlet and outlet flow, pressure, etc., as well as pump lift, efficiency, and shaft power curves.
[0034] Step 2) Set the boundary conditions according to the test data: the inlet flow rate is 25m3 / h and the outlet pressure is 330kPa. Model the fluid domain, calculate the f...
PUM
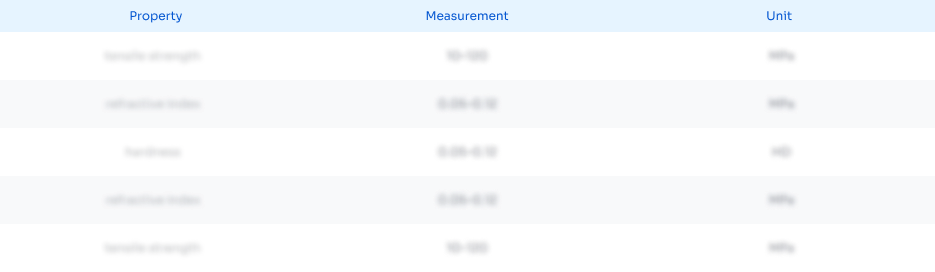
Abstract
Description
Claims
Application Information

- R&D
- Intellectual Property
- Life Sciences
- Materials
- Tech Scout
- Unparalleled Data Quality
- Higher Quality Content
- 60% Fewer Hallucinations
Browse by: Latest US Patents, China's latest patents, Technical Efficacy Thesaurus, Application Domain, Technology Topic, Popular Technical Reports.
© 2025 PatSnap. All rights reserved.Legal|Privacy policy|Modern Slavery Act Transparency Statement|Sitemap|About US| Contact US: help@patsnap.com