Mixing and coating technology for production of positive and negative pole pieces of lithium ion battery
A lithium-ion battery and coating process technology, applied in battery electrodes, electrode manufacturing, electrode extrusion, etc., can solve the problems of large consumption of NMP, long production process, high energy consumption, etc., and achieve the effect of saving energy and shortening the length
- Summary
- Abstract
- Description
- Claims
- Application Information
AI Technical Summary
Problems solved by technology
Method used
Examples
Embodiment Construction
[0012] Dissolve PVDF in NMP to form a 40% solution.
[0013] Weigh an appropriate amount of electrode active materials (lithium iron phosphate, lithium manganese oxide, lithium cobaltate, ternary materials, etc.) and conductive agent, and the solution obtained in step 1, and put them into the rough mixing equipment and mix for 20 minutes.
[0014] The coarsely mixed material is fed into the extruder through a screw feeder, and the temperature of the extruder is set to: 90°C for stage 1, 110°C for stage 2, and 110°C for stage 3. A filter that can be heated is connected to the outlet of the extruder, the temperature of the filter is 110° C., and the filter aperture is 200 mesh.
[0015] The filtered material from the extruder was directly directed to a transfer coater at a temperature of 110°C for coating.
[0016] The coated pole pieces are sent to a 20-meter-long oven for drying.
[0017] The finished product is wound, or directly connected to the rolling process.
PUM
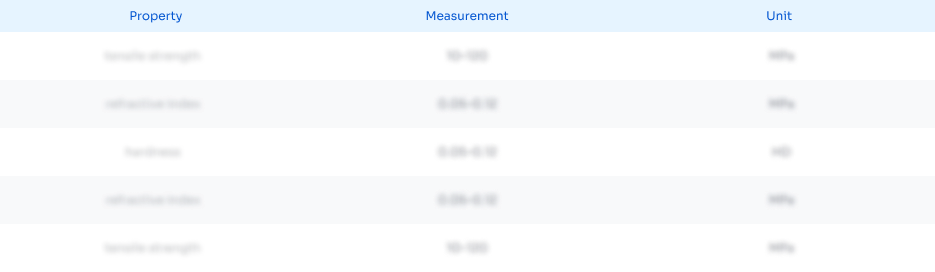
Abstract
Description
Claims
Application Information

- R&D Engineer
- R&D Manager
- IP Professional
- Industry Leading Data Capabilities
- Powerful AI technology
- Patent DNA Extraction
Browse by: Latest US Patents, China's latest patents, Technical Efficacy Thesaurus, Application Domain, Technology Topic, Popular Technical Reports.
© 2024 PatSnap. All rights reserved.Legal|Privacy policy|Modern Slavery Act Transparency Statement|Sitemap|About US| Contact US: help@patsnap.com