Middle propeller cavitation noise numerical prediction characteristic extraction method based on inhomogeneous inflow
A technology of feature extraction and numerical prediction, applied in the fields of electrical digital data processing, special data processing applications, instruments, etc., can solve the problems of no optimal cavitation model and turbulence model, and no good
- Summary
- Abstract
- Description
- Claims
- Application Information
AI Technical Summary
Problems solved by technology
Method used
Image
Examples
Embodiment 1
[0103] The E779A propeller is selected for verification by CFD calculation. The calculation domain is the whole channel area, and the hybrid grid division method is adopted. The rotation domain around the propeller is an unstructured grid, and the rest of the water domain is a structured grid. The distance from the upstream to the center of the propeller is 1D, and the distance from the downstream to the center of the propeller is 3.75D. The calculated cylindrical radius around the propeller is 1.471D, where D is the diameter of the propeller. Using slip grid technique and RNG turbulence model, ρ l =1000kg / m 3 , ρ v =0.02kg / m 3 , the surface tension coefficient γ=0.0717N / m, when the advancing speed coefficient J=0.71, calculate the cavitation index σ=1.763 and the thrust coefficient K when there is no cavitation T and moment coefficient 10K Q , see Table 1.
[0104] The non-uniform inflow axial velocity simulation uses the following formula:
[0105] u x =U 0 (f 1 f ...
Embodiment 2
[0114] To predict cavitation noise for DTMB4381 and DTMB4382 propellers, the mathematical formula in Embodiment 1 is used for non-uniform inflow. The side slope angles of DTMB4381 and DTMB4382 propellers are 0 degrees and 36 degrees respectively. When the advance speed coefficient J=0.9, the propeller speed n=30.5rps, the axial uniform inflow velocity is U 0 =6.22m / s, cavitation index σ=1.763, and p=44723pa, the circumferential distribution of cavitation of DTMB4381 propeller and DTMB4382 propeller blades is calculated, the radiation sound pressure is calculated, and the power spectral density is obtained, see Figure 8 , 9, 10.
Embodiment 3
[0116] The relevant experimental data and numerical results of a civil ship propeller are analyzed. The noise data is the sound pressure measured by the hydrophone at 2m directly below the propeller in the cavitation water tunnel. The sampling frequency is 195652Hz and the water velocity is 3.25m / s. The hydrostatic pressure in the cavitation water tunnel is 113000pa, and the noise and sound pressure data of the propeller speeds of 25rps and 28rps are measured respectively, and the measurement time is 5 seconds. The noise sound pressure power spectrum is as follows Figure 11 .
[0117] The uniform inflow velocity in the axial direction is U 0 =3.25m / s, p=113000pa, the propeller speeds are 25rps and 28rps respectively, and the iteration time of each step is 0.0005 seconds. The comparative verification of the slice cavitation area is as follows Figure 12 , calculate the circumferential distribution of blade cavitation, calculate the radiation sound pressure, and get the power ...
PUM
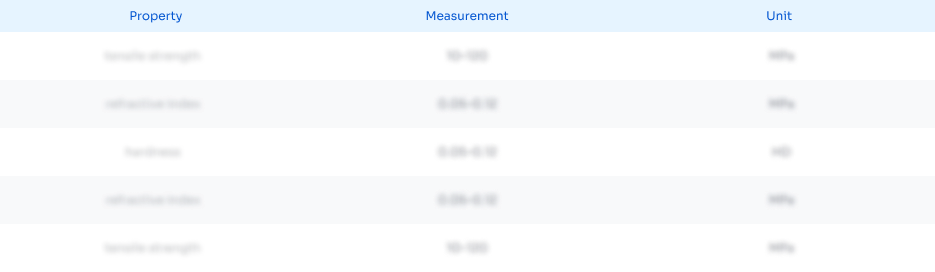
Abstract
Description
Claims
Application Information

- R&D
- Intellectual Property
- Life Sciences
- Materials
- Tech Scout
- Unparalleled Data Quality
- Higher Quality Content
- 60% Fewer Hallucinations
Browse by: Latest US Patents, China's latest patents, Technical Efficacy Thesaurus, Application Domain, Technology Topic, Popular Technical Reports.
© 2025 PatSnap. All rights reserved.Legal|Privacy policy|Modern Slavery Act Transparency Statement|Sitemap|About US| Contact US: help@patsnap.com