Side chain alkylation method of toluene with methanol
A technology of alkylation and methanol, applied in chemical instruments and methods, organic chemistry, hydrocarbons, etc., can solve the problems of low selectivity of ethylbenzene and styrene, low conversion rate of toluene, etc., to improve ion exchange degree, Good technical effect, the effect of improving the catalytic effect
- Summary
- Abstract
- Description
- Claims
- Application Information
AI Technical Summary
Problems solved by technology
Method used
Image
Examples
Embodiment 1~3
[0018] First, 5.27 grams of sodium metaaluminate (NaAlO 2 ) into 10.8 grams of water, heated and stirred to dissolve to obtain solution A. Then prepare sodium hydroxide and potassium hydroxide mixed alkali solution B according to the following ratio: [embodiment 1], 3.68 gram sodium hydroxide, 20.61 gram potassium hydroxide, 28 gram water; [embodiment 2], 7.36 gram hydroxide Sodium, 15.46 gram potassium hydroxide, 28 gram water; [embodiment 3], 11.04 gram sodium hydroxide, 10.30 gram potassium hydroxide, 28 gram water. Solution A was added to solution B with stirring to obtain solution C. 19.88 grams of sodium silicate (Na 2 SiO 3 9H 2 O) join in 20 grams of water, heat and stir to obtain solution D. Solution D was then added to Solution C with stirring. Transfer the mother liquor to a crystallization tank at 80°C for 1 hour and 93°C for 5 hours to crystallize to obtain crystals, and finally filter and dry the crystals to obtain molecular sieves. Feedstock composition d...
Embodiment 4~6
[0021] First, 5.27 grams of sodium metaaluminate (NaAlO 2 ) into 10.8 grams of water, heated and stirred to dissolve to obtain solution A. Then prepare sodium hydroxide and potassium hydroxide mixed alkali solution B according to the following ratio: [embodiment 4], 9.38 gram sodium hydroxide, 6.47 gram potassium hydroxide, 28 gram water; [embodiment 5], 7.50 gram hydroxide Sodium, 5.17 gram potassium hydroxide, 28 gram water; [embodiment 6], 5.63 gram sodium hydroxide, 3.89 gram potassium hydroxide, 28 gram water. Solution A was added to solution B with stirring to obtain solution C. 19.88 grams of sodium silicate (Na 2 SiO 3 9H 2 O) was added into 31.5 grams of water, heated and stirred to obtain solution D. Solution D was then added to Solution C with stirring. Transfer the mother liquor to a crystallization tank at 80°C for 1 hour and 93°C for 5 hours to crystallize to obtain crystals, and finally filter and dry the crystals to obtain molecular sieves.
[0022]
Embodiment 7
[0024] First, 3.16 grams of aluminum hydroxide was added to an alkaline solution containing 9.93 grams of potassium hydroxide and 11.33 grams of water, heated and stirred to dissolve to obtain solution A. Then prepare mixed alkali solution B of sodium hydroxide and potassium hydroxide according to the following ratio: 4.8 grams of sodium hydroxide, 10.08 grams of potassium hydroxide, and 47.6 grams of water. Solution A was added to solution B with stirring to obtain solution C. 7.8 grams of sodium silicate (Na 2 SiO 3 9H 2 O) join in 20g gram of water, heat and stir to obtain solution D. Solution D was then added to Solution C with stirring. Transfer the mother liquor to a crystallization tank at 70°C for 1 hour and 93°C for 40 hours to crystallize to obtain crystals, and finally filter and dry the crystals to obtain molecular sieves.
[0025]
PUM
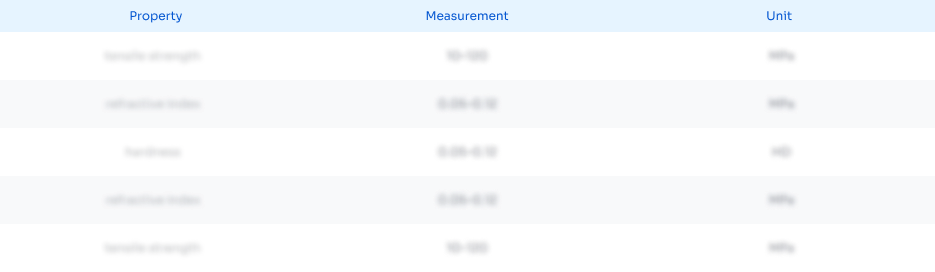
Abstract
Description
Claims
Application Information

- R&D
- Intellectual Property
- Life Sciences
- Materials
- Tech Scout
- Unparalleled Data Quality
- Higher Quality Content
- 60% Fewer Hallucinations
Browse by: Latest US Patents, China's latest patents, Technical Efficacy Thesaurus, Application Domain, Technology Topic, Popular Technical Reports.
© 2025 PatSnap. All rights reserved.Legal|Privacy policy|Modern Slavery Act Transparency Statement|Sitemap|About US| Contact US: help@patsnap.com