Automatic TPMS (Tire Pressure Monitor System) tire positioning method and system
An automatic positioning and tire technology, applied in tire measurement, tire parts, transportation and packaging, etc., can solve the problems of detection errors, high cost, inconvenience, etc., to reduce production costs, improve production efficiency, and accurate and reliable positioning structure. Effect
- Summary
- Abstract
- Description
- Claims
- Application Information
AI Technical Summary
Problems solved by technology
Method used
Image
Examples
Embodiment Construction
[0030] Below in conjunction with accompanying drawing and specific embodiment, the present invention will be further described:
[0031] See figure 1 , the present invention relates to a kind of TPMS tire position automatic positioning method, and its preferred embodiment comprises the following steps:
[0032] Tire status information receiving step: receiving tire status information from each TPMS sensor assembly, each tire status information includes vehicle speed value, acceleration value of each X-axis acceleration sensor, temperature value of each temperature sensor and air pressure value of each air pressure sensor. Wherein, the TPMS sensor assembly includes at least a microprocessor, a temperature sensor, an air pressure sensor, an X-axis acceleration sensor and a radio frequency signal transceiver module, and the installation and connection relationship of each component of the TPMS sensor assembly can be known from the prior art, for example, the In front of the X-ax...
PUM
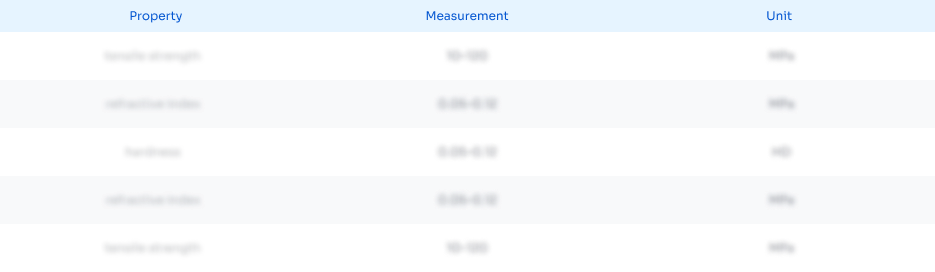
Abstract
Description
Claims
Application Information

- Generate Ideas
- Intellectual Property
- Life Sciences
- Materials
- Tech Scout
- Unparalleled Data Quality
- Higher Quality Content
- 60% Fewer Hallucinations
Browse by: Latest US Patents, China's latest patents, Technical Efficacy Thesaurus, Application Domain, Technology Topic, Popular Technical Reports.
© 2025 PatSnap. All rights reserved.Legal|Privacy policy|Modern Slavery Act Transparency Statement|Sitemap|About US| Contact US: help@patsnap.com