Method for forecasting noise value of propeller in uneven inflow
A numerical forecasting and propeller technology, applied in electrical digital data processing, special data processing applications, instruments, etc., can solve problems such as few successful simulations, no better cavitation model and turbulence model
- Summary
- Abstract
- Description
- Claims
- Application Information
AI Technical Summary
Problems solved by technology
Method used
Image
Examples
Embodiment 1
[0119] The verified propeller model is a DTMB4119 propeller, a three-blade propeller with no skew and no pitch distribution, the propeller diameter is 0.305m, the disk-to-surface ratio is 0.6, the blade cut surface is NACA-66, and the hub diameter ratio is 0.2. The CFD calculation area model is as follows: the upstream distance is 0.7D, the downstream distance is 3.75D, the radius of the rotating area is 0.16165m, the length is 0.14m, the radius of the static area is 1.471D, Gambit is used to divide the grid, and the rotating area is For unstructured grid division, the number of grids is 572382, and the static area is divided into structured grids, with the number of grids being 1762748. The parameters for CFD calculation are set as follows: the static pressure is 101325Pa, the inlet inflow velocity is 5.808m / s, the propeller speed is 20rps, the sliding grid technology is adopted, and the k-εRNG model is used for the turbulence model. The value comparison is shown in Table 1. ...
Embodiment 2
[0128] The geometric parameters of a civil ship propeller are as follows: the number of blades is 4, the diameter of the propeller is 0.2482m, the disc-to-surface ratio is 0.55, and the side slope angle is 32 degrees.
[0129] Figure 7 This is the comparison and verification diagram of the cavitation simulation of the circumferential blade of the civilian ship propeller, and the uniform inflow velocity U in the axial direction is 0 is 3.25m / s, the ambient pressure is 113000Pa, the propeller speed n is 25rps and 28rps respectively, and the iteration time of each step is 0.0005 seconds. The advance coefficients J corresponding to the two different speeds are 0.5238 and 0.4677 respectively, and the cavitation exponents σ are respectively 5.747, 4.58, calculate the radiation sound pressure of the blade cavitation monopole sound source, where r=1. Figure 9 It is the sound pressure distribution map within 0.04 seconds of a propeller rotation. Spectrograms of cavitation noise sou...
PUM
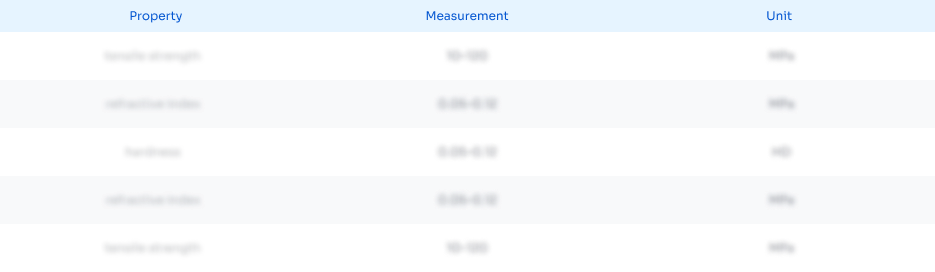
Abstract
Description
Claims
Application Information

- Generate Ideas
- Intellectual Property
- Life Sciences
- Materials
- Tech Scout
- Unparalleled Data Quality
- Higher Quality Content
- 60% Fewer Hallucinations
Browse by: Latest US Patents, China's latest patents, Technical Efficacy Thesaurus, Application Domain, Technology Topic, Popular Technical Reports.
© 2025 PatSnap. All rights reserved.Legal|Privacy policy|Modern Slavery Act Transparency Statement|Sitemap|About US| Contact US: help@patsnap.com