Flexural rigidity testing device in copious cooling and high-temperature environments
A high-temperature environment, bending stiffness technology, applied in the direction of testing the strength of materials by applying a stable bending force, can solve the problem that the laser emitter cannot be located on the component and follow the three-dimensional displacement of a certain point, and achieve accurate measurement of the deflection angle Deformation, good real-time performance, and high measurement accuracy
- Summary
- Abstract
- Description
- Claims
- Application Information
AI Technical Summary
Problems solved by technology
Method used
Image
Examples
Embodiment Construction
[0026] combine Figure 1 to Figure 2 , Bending stiffness testing device under cryogenic and high temperature environment, including laser displacement sensor 7, high stiffness rod 6, corner mirror 4, laser measurement group, force sensor 10, lifting device 11 and so on.
[0027] The DUT 3 and its mounting base 2 are placed in a high and low temperature box, one end of the high rigidity rod 6 is fixedly connected to the lifting device 11, and the other end of the high rigidity rod 6 is a smooth spherical surface and vertical Directly acting on the tested object 3, a force sensor 10 is installed between the high rigidity rod 6 and the lifting device 11.
[0028] The laser displacement sensor 7 is installed outside the high and low temperature box 1, the measurement direction of the laser displacement sensor 7 is parallel to the direction of the force arm, and the measurement point of the laser displacement sensor 7 is close to the DUT 3 and the DUT mounting seat 2 the roots.
...
PUM
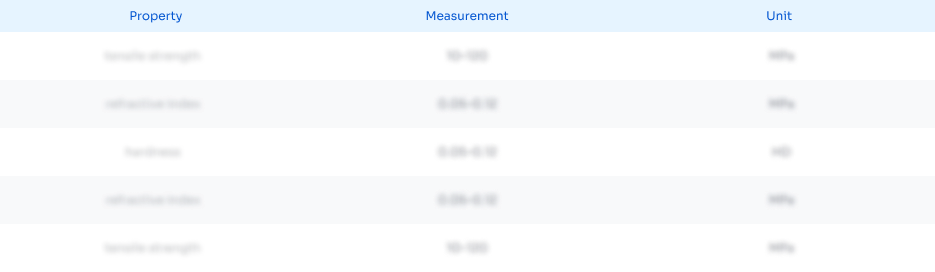
Abstract
Description
Claims
Application Information

- R&D
- Intellectual Property
- Life Sciences
- Materials
- Tech Scout
- Unparalleled Data Quality
- Higher Quality Content
- 60% Fewer Hallucinations
Browse by: Latest US Patents, China's latest patents, Technical Efficacy Thesaurus, Application Domain, Technology Topic, Popular Technical Reports.
© 2025 PatSnap. All rights reserved.Legal|Privacy policy|Modern Slavery Act Transparency Statement|Sitemap|About US| Contact US: help@patsnap.com