Engine vibration and engine trim balance test system, apparatus and method
An engine and vibration velocity technology, applied in the simulation field of aircraft engine test, can solve problems such as manual calculation
- Summary
- Abstract
- Description
- Claims
- Application Information
AI Technical Summary
Problems solved by technology
Method used
Image
Examples
Embodiment Construction
[0015] The following detailed description aims to provide a system of maximum capability that allows aircraft-level integration of test line replaceable units (LRUs) that monitor engine vibration. Typical LRUs with this capability include an Airborne Vibration Monitor (AVM) installed within the aircraft's avionics, an Engine Monitoring Unit (EMU) mounted on the engine, and a Health and Usage Monitoring System (HUMS) in the propeller aircraft , but the LRU list is not exhaustive, and alternative semantics exist. The design of the system can be applied or adapted to similar LRUs installed on other engines / aircraft types / propeller aircraft. Aircraft-level integration testing focuses on verification and validation of engine indication displays, events, messages, and interaction with diagnostics and predictive maintenance operations related to engine vibration systems. The LRU measures vibrations in the aircraft engine 12 using accelerometers. refer to figure 1 and figure 2 , ...
PUM
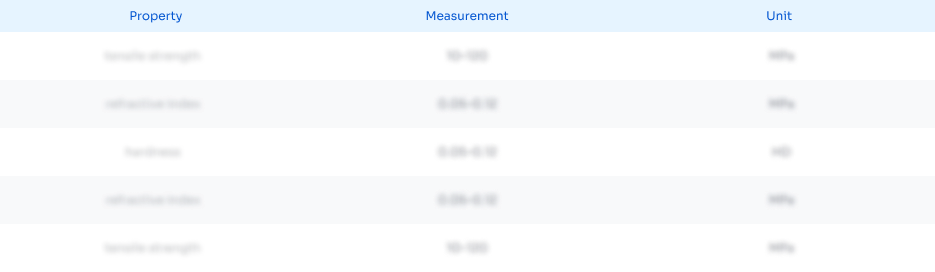
Abstract
Description
Claims
Application Information

- R&D
- Intellectual Property
- Life Sciences
- Materials
- Tech Scout
- Unparalleled Data Quality
- Higher Quality Content
- 60% Fewer Hallucinations
Browse by: Latest US Patents, China's latest patents, Technical Efficacy Thesaurus, Application Domain, Technology Topic, Popular Technical Reports.
© 2025 PatSnap. All rights reserved.Legal|Privacy policy|Modern Slavery Act Transparency Statement|Sitemap|About US| Contact US: help@patsnap.com