Catalytic converter assembly welding method for vehicle exhaust system
An assembly welding method and an automobile exhaust system technology, applied in welding equipment, welding equipment, auxiliary welding equipment, etc., can solve problems such as uncontrollable deformation, difficult product quality assurance, and complicated operation
- Summary
- Abstract
- Description
- Claims
- Application Information
AI Technical Summary
Problems solved by technology
Method used
Image
Examples
Embodiment Construction
[0025] see Figure 7 , the catalytic converter assembly consists of a front flange 1, a front connecting pipe 2, a front cone 3, a carrier shell 5, a rear cone 6, a middle connecting pipe 7, a soft connection 8, a rear connecting pipe 9, and a rear flange 10. The parts are welded into one body through eight welds, and the oxygen sensing nut 4 is arranged on the front cone. The shape of the catalytic converter assembly is irregular, and it also includes soft connections. It is difficult to position during the welding process. It is difficult to ensure the size and position of the product. It is difficult to control the shrinkage of the welded parts. In addition, the heat of the pipe body will cause serious deformation of the assembly. , resulting in poor consistency of the workpiece after welding, making it difficult to meet the requirements for the assembly position accuracy of the catalytic converter assembly. For a long time, no matter the method of spot welding each componen...
PUM
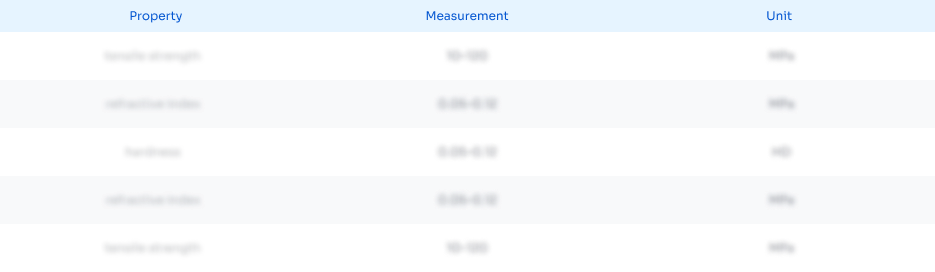
Abstract
Description
Claims
Application Information

- R&D
- Intellectual Property
- Life Sciences
- Materials
- Tech Scout
- Unparalleled Data Quality
- Higher Quality Content
- 60% Fewer Hallucinations
Browse by: Latest US Patents, China's latest patents, Technical Efficacy Thesaurus, Application Domain, Technology Topic, Popular Technical Reports.
© 2025 PatSnap. All rights reserved.Legal|Privacy policy|Modern Slavery Act Transparency Statement|Sitemap|About US| Contact US: help@patsnap.com