Forming mold for aircraft skin part
A technology for forming molds and skins, applied in the field of metal pressure processing, can solve the problems of difficulty in shape calibration, affecting the surface quality and shape accuracy of the skin, and difficult to control, so as to improve the forming accuracy and surface quality, and prevent complex surfaces from being covered. The effect of skin suspension, improving integrity and compounding
- Summary
- Abstract
- Description
- Claims
- Application Information
AI Technical Summary
Problems solved by technology
Method used
Image
Examples
Embodiment Construction
[0046] In the following detailed description of the embodiments, reference is made to the accompanying drawings that form a part hereof. The drawings show, by way of example, specific embodiments in which the invention may be practiced. The illustrated embodiments are not intended to be exhaustive of all embodiments according to the invention. It is to be understood that other embodiments may be utilized and structural or logical changes may be made without departing from the scope of the present invention. With respect to the drawings, directional terms, such as "lower," "upper," etc., are used with reference to the orientation of the drawings being described. Since components of embodiments of the invention can be implemented in a variety of orientations, these directional terms are used for purposes of description, not limitation. Accordingly, the following detailed description is not intended to be limiting, and the scope of the invention is defined by the appended claim...
PUM
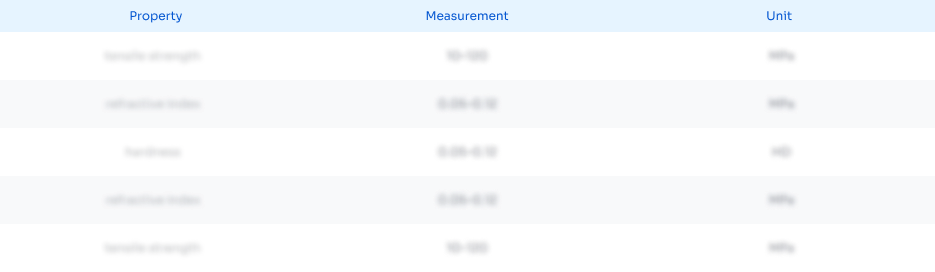
Abstract
Description
Claims
Application Information

- R&D
- Intellectual Property
- Life Sciences
- Materials
- Tech Scout
- Unparalleled Data Quality
- Higher Quality Content
- 60% Fewer Hallucinations
Browse by: Latest US Patents, China's latest patents, Technical Efficacy Thesaurus, Application Domain, Technology Topic, Popular Technical Reports.
© 2025 PatSnap. All rights reserved.Legal|Privacy policy|Modern Slavery Act Transparency Statement|Sitemap|About US| Contact US: help@patsnap.com