System and method for calculating driving torque of wind driven generator yaw system
A technology for wind turbines and yaw systems, which is applied in computing, electrical digital data processing, special data processing applications, etc., can solve the problems of noise, complex wind alternating loads, uneven pressure distribution between friction plates and yaw ring gears, etc. , to achieve the effect of reducing cost and facilitating power optimization selection
- Summary
- Abstract
- Description
- Claims
- Application Information
AI Technical Summary
Problems solved by technology
Method used
Image
Examples
Embodiment Construction
[0027] For the sake of reference and clarity, the technical terms, abbreviations or abbreviations used below are recorded as follows:
[0028] Abaqus: It is a set of powerful engineering simulation finite element software, which can solve problems ranging from relatively simple linear analysis to many complex nonlinear problems. It is a collaborative, open and integrated multi-physics simulation platform;
[0029] Ansys: It is a large-scale general-purpose finite element analysis software integrating structure, fluid, electric field, magnetic field, and sound field analysis. It is developed by American ANSYS, one of the largest finite element analysis software companies in the world. It can interface with most CAD software to realize Data sharing and exchange, such as Pro / Engineer, NASTRAN, Alogor, I-DEAS, AutoCAD, etc., is one of the advanced CAE tools in modern product design.
[0030] In order to make the purpose, technical solutions and advantages of the embodiments of the...
PUM
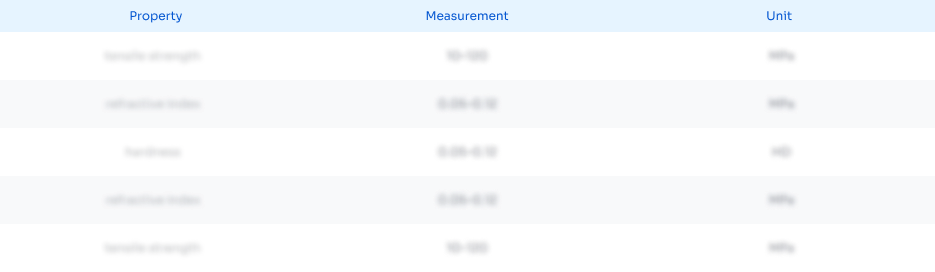
Abstract
Description
Claims
Application Information

- R&D
- Intellectual Property
- Life Sciences
- Materials
- Tech Scout
- Unparalleled Data Quality
- Higher Quality Content
- 60% Fewer Hallucinations
Browse by: Latest US Patents, China's latest patents, Technical Efficacy Thesaurus, Application Domain, Technology Topic, Popular Technical Reports.
© 2025 PatSnap. All rights reserved.Legal|Privacy policy|Modern Slavery Act Transparency Statement|Sitemap|About US| Contact US: help@patsnap.com