Method for preparing high-reflectance working mould of microprism reflecting films by utilizing ultrasonic electroforming
A technology of reflectivity and micro-prism, applied in the field of micro-prism, can solve the problem of difficulty in controlling the reflectivity of the working mode of the reflective film, and achieve the effect of convenient adjustment
- Summary
- Abstract
- Description
- Claims
- Application Information
AI Technical Summary
Problems solved by technology
Method used
Image
Examples
Embodiment 1
[0021] Preparation of electroforming solution: According to the total volume of the electroforming tank, weigh 450g of nickel sulfate, 50g of nickel chloride, 50g of boric acid, 0.07g of sodium lauryl sulfate, 0.5g of saccharin and 0.35g of 1,4-butynediol. g. Add deionized water to the electroforming tank, heat to 50°C, add weighed nickel sulfate and nickel chloride in turn, stir and keep warm for 4 hours. Take another beaker and rinse it with deionized water, dry it, add deionized water, stir and heat to boiling, add weighed boric acid and boil for 0.5h, then add sodium lauryl sulfate, wait until sodium lauryl sulfate is fully dissolved Finally, slowly pour it into the electroforming tank, and add saccharin and butynediol to the casting tank, then add deionized water until the electroforming tank is full, stir well, keep warm at 45°C for 12 hours, and measure with pH test paper Its pH value is adjusted to pH=4.2 with 30% sulfuric acid solution. Guaranteed quality-volume con...
Embodiment 2
[0028] Preparation of nickel sulfate electroforming solution: according to the total volume of the electroforming tank, first weigh 300g of nickel sulfate, 30g of nickel chloride, 30g of boric acid, 0.05g of sodium lauryl sulfate, 0.1g of saccharin and 1,4-butynedi Alcohol 0.2g. Add deionized water to the electroforming tank, heat to 55°C, add weighed nickel sulfate and nickel chloride in turn, stir and keep warm for 3.5h. Take another beaker and rinse it with deionized water, dry it, add deionized water, stir and heat to boiling, add weighed boric acid and boil for 40min, then add sodium lauryl sulfate, after sodium lauryl sulfate is fully dissolved , slowly pour it into the electroforming tank, and add saccharin and butynediol into the casting tank, then add deionized water until the electroforming tank is full, stir well, keep warm at 50°C for 10 hours, and measure the pH value with pH test paper pH value, adjusted to pH=4.2 with 30% sulfuric acid solution. Guaranteed qua...
Embodiment 3
[0034]Preparation of nickel sulfate electroforming solution: According to the total volume of the electroforming tank, first weigh 600g of nickel sulfate, 70g of nickel chloride, 75g of boric acid, 1g of sodium lauryl sulfate, 1g of saccharin and 0.5 g of 1,4-butynediol g. Add 1 / 2 volume of deionized water to the electroforming tank, heat to 60°C, add weighed nickel sulfate and nickel chloride in turn, stir and keep warm for 3 hours. Take another beaker and rinse it with deionized water, dry it, add deionized water, stir and heat to boiling, add weighed boric acid and boil for 50 minutes, then add sodium lauryl sulfate, after sodium lauryl sulfate is fully dissolved , slowly pour it into the electroforming tank, and add saccharin and butynediol to the casting tank, then add deionized water until the electroforming tank is full, stir well, keep it warm at 55°C for 8 hours, and measure it with pH test paper pH value, adjusted to pH=4.2 with 30% sulfuric acid solution. Guarante...
PUM
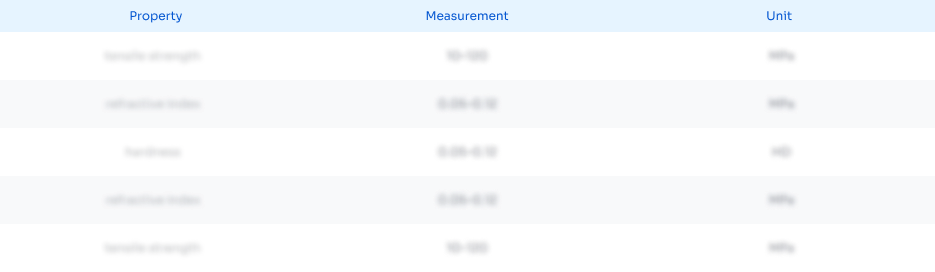
Abstract
Description
Claims
Application Information

- R&D Engineer
- R&D Manager
- IP Professional
- Industry Leading Data Capabilities
- Powerful AI technology
- Patent DNA Extraction
Browse by: Latest US Patents, China's latest patents, Technical Efficacy Thesaurus, Application Domain, Technology Topic, Popular Technical Reports.
© 2024 PatSnap. All rights reserved.Legal|Privacy policy|Modern Slavery Act Transparency Statement|Sitemap|About US| Contact US: help@patsnap.com