A two-finger translational manipulator
A manipulator and translation technology, applied in the field of robotics, can solve problems such as difficulty in grasping workpieces that are too large or too small, difficulty in adjusting the distance between finger roots, high requirements for installation and use, and achieve simple structure, strong adaptability, The effect of enhancing the ability to grasp workpieces
- Summary
- Abstract
- Description
- Claims
- Application Information
AI Technical Summary
Problems solved by technology
Method used
Image
Examples
Embodiment Construction
[0013] Further illustrate the present invention below in conjunction with accompanying drawing.
[0014] refer to Figure 1-Figure 5 , the structure of the two-finger translation manipulator of the present invention includes: palm base 1, steering gear 2, left finger gear 3, two transmission gears 4, left finger translation rack 5, left finger root 6, right finger root 7 , two micro switches 8, two recovery springs 9, right finger gear 10, right finger translation rack 11, right finger 12, left finger 13, four gear shafts 14, steering frame 16, rubber skin 19 and balls bearing 20.
[0015] Servo 2 (see figure 1 ) is installed above the palm base 1 through the steering rack 16, and the palm base 1 (see Figure 6 ) There are two horizontally protruding rack guide rails 17 on the upper and lower inner surfaces of the front part, and there are two transversely recessed teeth on the lower plane of the left finger translation rack 5 and the upper plane of the right finger transla...
PUM
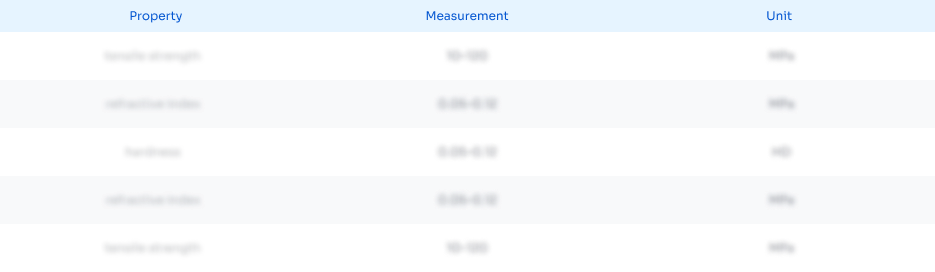
Abstract
Description
Claims
Application Information

- R&D
- Intellectual Property
- Life Sciences
- Materials
- Tech Scout
- Unparalleled Data Quality
- Higher Quality Content
- 60% Fewer Hallucinations
Browse by: Latest US Patents, China's latest patents, Technical Efficacy Thesaurus, Application Domain, Technology Topic, Popular Technical Reports.
© 2025 PatSnap. All rights reserved.Legal|Privacy policy|Modern Slavery Act Transparency Statement|Sitemap|About US| Contact US: help@patsnap.com