Charging member, process cartridge, and electrophotographic apparatus
A charging member, electrophotography technology, applied to equipment, electrical components, corona discharge devices, etc. that apply the electric recording process of the charge pattern, and can solve the problem of stably charging the photosensitive member to a specified potential, reducing the level of electrophotographic images, etc. question
- Summary
- Abstract
- Description
- Claims
- Application Information
AI Technical Summary
Problems solved by technology
Method used
Image
Examples
preparation example 1
[0124] [Preparation Example 1] Preparation of Composite Conductive Fine Particles
[0125] 140g of methyl hydrogen polysiloxane was added to 7.0kg of silica particles (number average particle diameter: 15nm, volume resistivity: 1.8×10 12 Ω·cm), operate the wheel mill. These materials were then mixed and stirred for 30 minutes under a linear load of 588 N / cm (60 kg / cm). Here, stirring was performed at a speed of 22 rpm. Add 7.0kg of carbon black particles (number-average particle diameter: 20nm, volume resistivity: 1.0×10) through the time of 10 minutes in the material stirred like this 2 Ω·cm, pH: 8.0), operating the wheel mill, these materials were further mixed, and stirred under a linear load of 588 N / cm (60 kg / cm) for 60 minutes.
[0126]Thus, carbon black was allowed to adhere to the surface of the silica particles that had been coated with methylhydrogenpolysiloxane, and then dried by a drier at 80° C. for 60 minutes to obtain composite conductive fine particles. Her...
preparation example 2
[0127] [Preparation Example 2] Preparation of surface-treated titanium oxide particles
[0128] 1000g of acicular rutile titanium oxide particles (number average particle diameter: 15nm, length / width=3:1, volume resistivity: 2.3×10 10 Ω·cm) was mixed with 110 g of isobutyltrimethoxysilane as a surface treatment agent and 3000 g of toluene as a solvent to prepare a slurry. The slurry was mixed by a stirrer for 30 minutes, and then supplied to a Visco mill filled with 80% of the effective internal volume of glass beads having a number average particle diameter of 0.8 mm, thereby performing a wet process at a temperature of 35±5°C. Shred processing.
[0129] The slurry obtained by wet disintegration treatment was distilled under reduced pressure by using a kneader (bath temperature: 110°C, product temperature: 30°C to 60°C, degree of reduced pressure: about 100 Torr) to remove toluene, and then surface treated The agent was fired at 120°C for 2 hours. The particles that had be...
Embodiment 1
[0131] [substrate]
[0132] A substrate made of stainless steel with a diameter of 6 mm and a length of 252.5 mm was coated with a thermosetting binder containing 10% by mass of carbon black, and then dried.
[0133] [Material for the first rubber layer]
[0134] The materials shown in Table 1 below were kneaded using an internal mixer controlled at a temperature of 50° C. to obtain an unvulcanized rubber composition.
[0135] [Table 1]
[0136]
[0137] Next, 1.2 parts by mass of sulfur as a vulcanizing agent and 1 part by mass of dibenzothiazole vulcanization (DM) and 1 part by mass of tetramethylsulfuric acid as a vulcanization accelerator were added to 178.5 parts by mass of the above-mentioned unvulcanized rubber composition. Lamb (TS), these materials were kneaded for 10 minutes by a two-roll mill kept at a temperature cooled to 20° C., thereby obtaining a material for the first rubber layer.
[0138] [Material for the second rubber layer]
[0139] The materials s...
PUM
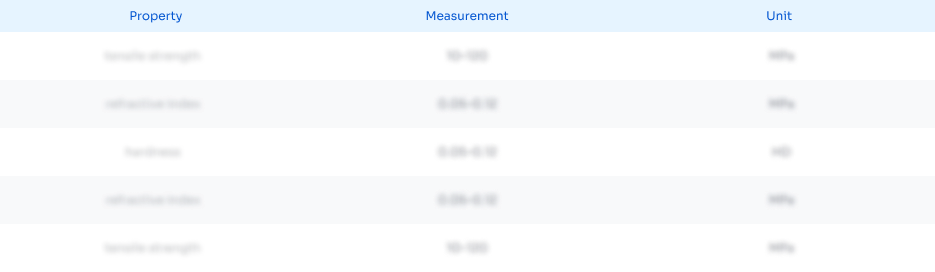
Abstract
Description
Claims
Application Information

- R&D
- Intellectual Property
- Life Sciences
- Materials
- Tech Scout
- Unparalleled Data Quality
- Higher Quality Content
- 60% Fewer Hallucinations
Browse by: Latest US Patents, China's latest patents, Technical Efficacy Thesaurus, Application Domain, Technology Topic, Popular Technical Reports.
© 2025 PatSnap. All rights reserved.Legal|Privacy policy|Modern Slavery Act Transparency Statement|Sitemap|About US| Contact US: help@patsnap.com