Compound microcapsule wall material and application thereof in essence microcapsules for cigarettes
A technology of microcapsule wall material and essence microcapsules, applied in the directions of essential oils/spices, fat generation, etc., can solve the problems of high price, difficult to achieve embedding effect, etc., achieve low moisture content, prolong retention time, high encapsulation Buried rate effect
- Summary
- Abstract
- Description
- Claims
- Application Information
AI Technical Summary
Problems solved by technology
Method used
Examples
Embodiment 1
[0017] The composite microcapsule wall material 1 of the present invention is formed by mixing the following components by mass percentage: 45.0% octenyl succinic esterified starch, 20.0% maltodextrin, 15.0% sodium carboxymethyl starch, 12.0% % soybean protein isolate, 2.0% gum arabic, 3.0% sodium caseinate, 2.0% sucrose, 0.2% sodium alginate, 0.3% xanthan gum, 0.5% pullulan.
[0018] Take 60g of composite wall material 1 and dissolve it in 340mL of water to form a wall material solution, stir well and add 12g of California lemon oil. First use a high-speed emulsifying homogenizer to shear at 15,000 rpm for 2 minutes; then use an ultra-high pressure micro-jet homogenizer to process once at a pressure of 35 MPa. The obtained emulsion was subjected to spray drying treatment, the inlet air temperature was 180°C, the outlet air temperature was 80°C, and the feed rate was 5mL / min. Collect California lemon oil microcapsule products and keep them sealed.
[0019] The California lem...
Embodiment 2
[0021] The composite microcapsule wall material 2 of the present invention is formed by mixing the following components by mass percentage: 30.0% octenyl succinic esterified starch, 30.0% maltodextrin, 20.0% sodium carboxymethyl starch, 15.0% % Soy Protein Isolate, 1.0% Gum Arabic, 2.0% Sodium Caseinate, 1.0% Sucrose, 0.4% Sodium Alginate, 0.5% Xanthan Gum, 0.1% Pullulan.
[0022] Take 80g of composite wall material 2 and dissolve it in 320mL of water to form a wall material solution, stir well and add 12g of clove bud oil. First use a high-speed emulsifying homogenizer to shear at 10,000rpm for 3 minutes; then use an ultra-high pressure micro-jet homogenizer to process twice at a pressure of 25MPa. The obtained emulsion was subjected to spray drying treatment, the inlet air temperature was 175°C, the outlet air temperature was 70°C, and the feed rate was 7mL / min. Collect clove bud oil microcapsule products and seal them for preservation.
[0023] The clove flower bud oil mi...
Embodiment 3
[0025] The composite microcapsule wall material 3 of the present invention is formed by mixing the following components by mass percentage: 30.0% octenyl succinic esterified starch, 15.0% maltodextrin, 30.0% sodium carboxymethyl starch, 10.0% % soybean protein isolate, 5.0% gum arabic, 5.0% sodium caseinate, 3.9% sucrose, 0.1% sodium alginate, 0.5% xanthan gum, 0.5% pullulan.
[0026] Take 70g of composite wall material 3 and dissolve it in 230mL of water to form a wall material solution, stir well and add 10g of cumin oil. First use a high-speed emulsifying homogenizer to shear at 12,000 rpm for 2 minutes; then use an ultra-high pressure micro-jet homogenizer to process twice at a pressure of 25 MPa. The obtained emulsion was subjected to spray drying treatment, the inlet air temperature was 165°C, the outlet air temperature was 75°C, and the feed rate was 9mL / min. Collect cumin oil microcapsule products and keep them sealed.
[0027] The fennel oil microcapsule product obt...
PUM
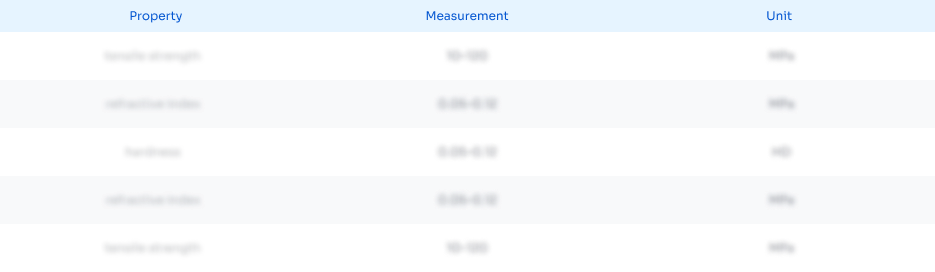
Abstract
Description
Claims
Application Information

- R&D
- Intellectual Property
- Life Sciences
- Materials
- Tech Scout
- Unparalleled Data Quality
- Higher Quality Content
- 60% Fewer Hallucinations
Browse by: Latest US Patents, China's latest patents, Technical Efficacy Thesaurus, Application Domain, Technology Topic, Popular Technical Reports.
© 2025 PatSnap. All rights reserved.Legal|Privacy policy|Modern Slavery Act Transparency Statement|Sitemap|About US| Contact US: help@patsnap.com