Low-viscosity alkoxy terminated polysiloxane and preparation method thereof
A technology of viscosity alkoxy-capped and alkoxysilane, which is applied in the field of low-viscosity alkoxy-capped polysiloxane and its preparation, can solve the problems of unstable product performance, catalyst residue, low yield, etc., and achieve Improve mechanical properties, stable performance, and solve the effect of oil leakage
- Summary
- Abstract
- Description
- Claims
- Application Information
AI Technical Summary
Problems solved by technology
Method used
Image
Examples
Embodiment 1
[0031] Raw material weight ratio:
[0032] α, ω-dihydroxypolydimethylsiloxane: 75 parts, dimethoxydimethylsilane: 25 parts.
[0033] Preparation: In a reaction vessel, add 75 parts of α, ω-dihydroxy polydimethylsiloxane, 25 parts of dimethoxydimethylsilane and 15 parts of catalyst alkali gel, start stirring (50rpm), and heat up to React at 90°C for 2.5 hours, then vacuumize at 160°C to remove low molecular weight for 2.5 hours to obtain low-viscosity alkoxy-terminated polysiloxane.
Embodiment 2
[0035] Proportion by weight of raw materials: α, ω-dihydroxy polydimethylsiloxane: 80 parts, dimethoxydimethylsilane: 20 parts.
[0036] Preparation: In a reaction vessel, add 80 parts of α, ω-dihydroxypolydimethylsiloxane, 20 parts of dimethoxydimethylsilane and 10 parts of catalyst alkali gel, start stirring (100rpm), and heat up to React at 100°C for 22 hours, then vacuumize at 170°C for 2 hours to remove the low molecular weight, and obtain low-viscosity alkoxy-terminated polysiloxane.
Embodiment 3
[0038] Proportion by weight of raw materials: α, ω-dihydroxy polydimethylsiloxane: 70 parts, dimethoxydimethylsilane: 30 parts.
[0039] Preparation: In a reaction vessel, add 70 parts of α, ω-dihydroxypolydimethylsiloxane, 30 parts of dimethoxydimethylsilane and 20 parts of catalyst alkali gel, start stirring (10rpm), and heat up to React at 100°C for 22 hours, then vacuumize at 170°C for 2 hours to remove the low molecular weight, and obtain low-viscosity alkoxy-terminated polysiloxane.
PUM
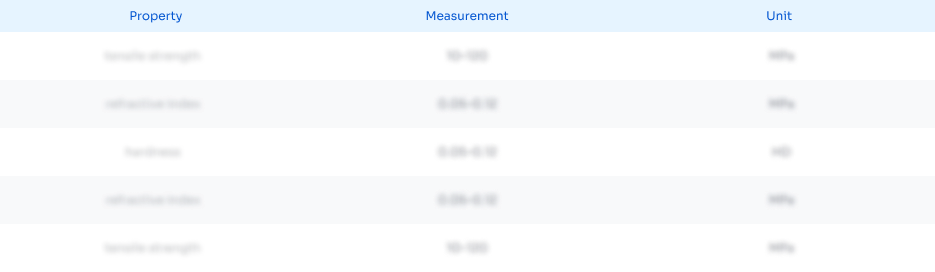
Abstract
Description
Claims
Application Information

- R&D
- Intellectual Property
- Life Sciences
- Materials
- Tech Scout
- Unparalleled Data Quality
- Higher Quality Content
- 60% Fewer Hallucinations
Browse by: Latest US Patents, China's latest patents, Technical Efficacy Thesaurus, Application Domain, Technology Topic, Popular Technical Reports.
© 2025 PatSnap. All rights reserved.Legal|Privacy policy|Modern Slavery Act Transparency Statement|Sitemap|About US| Contact US: help@patsnap.com