Down-hole rotary impact type drilling tool
A drilling tool and percussive technology, applied in the field of oil drilling tool design, can solve the problems that the drill bit is easy to form deflection moment, high rotational speed, and drill bit failure, so as to reduce the possibility of drill bit failure, improve the comprehensive technical and economic benefits, and improve the The effect of ROP
- Summary
- Abstract
- Description
- Claims
- Application Information
AI Technical Summary
Problems solved by technology
Method used
Image
Examples
Embodiment Construction
[0009] The downhole rotary impact drilling tool of the present invention consists of a flow sleeve 1, an upper shell 2, a spindle lock nut 3, an upper TC radial bearing 4, a rolling ball bearing group 5, an upper transmission spindle 6, an intermediate joint 7, and a spline sleeve 8. , Nozzle 9, Disc spring 10, Middle housing 11, Vibration sleeve 12, Vibration seat 13, Connecting sleeve 14, Impact head 15, Bearing seat 16, Separating sleeve 17, PDC bearing 18, Lower TC radial bearing moving ring 19. The lower TC radial bearing static ring 20, the lower joint 21, and the lower drive spindle 22 are composed; the upper end of the upper casing 2 is connected to the casing of the turbine motor, screw motor or electric motor; the lower end of the upper casing 2 is connected to the middle joint 7 The upper end of the middle joint 7 is connected with the upper end of the middle shell 11 by threads; the lower end of the middle shell 11 is connected with the lower joint 21 by threads; the...
PUM
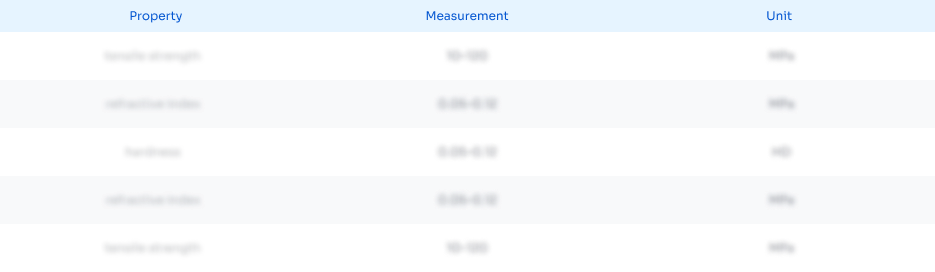
Abstract
Description
Claims
Application Information

- R&D
- Intellectual Property
- Life Sciences
- Materials
- Tech Scout
- Unparalleled Data Quality
- Higher Quality Content
- 60% Fewer Hallucinations
Browse by: Latest US Patents, China's latest patents, Technical Efficacy Thesaurus, Application Domain, Technology Topic, Popular Technical Reports.
© 2025 PatSnap. All rights reserved.Legal|Privacy policy|Modern Slavery Act Transparency Statement|Sitemap|About US| Contact US: help@patsnap.com