Calibration method oriented towards coaxial counterpoint micro-assembly system
A calibration method and micro-assembly technology, which can be applied to measurement devices, optical devices, instruments, etc., can solve problems such as being unsuitable for coaxial alignment micro-assembly systems, and achieve the effect of being simple and easy to implement and improving assembly accuracy.
- Summary
- Abstract
- Description
- Claims
- Application Information
AI Technical Summary
Problems solved by technology
Method used
Image
Examples
Embodiment Construction
[0028] Below in conjunction with accompanying drawing and embodiment the present invention will be described in further detail: the flow process of the inventive method is as follows figure 1 shown. The principle of the coaxial alignment optical system in this embodiment is as follows figure 2 As shown, it includes a CCD camera and a microscope lens, an optical prism, a substrate stage, a target stage, and an angular displacement stage 1, an angular displacement stage 2, and an angular displacement stage 3. Due to the existence of the coaxial optical prism, the parts on the substrate stage and the target stage enter the image plane of the camera at the same time, and the edge recognition is performed on the two images respectively, and the pose deviation of the part is calculated, and the deviation is compensated to the substrate carrier The six-degree-of-freedom motion platform under the stage, after the compensation is completed, withdraws the prism, and the target stage m...
PUM
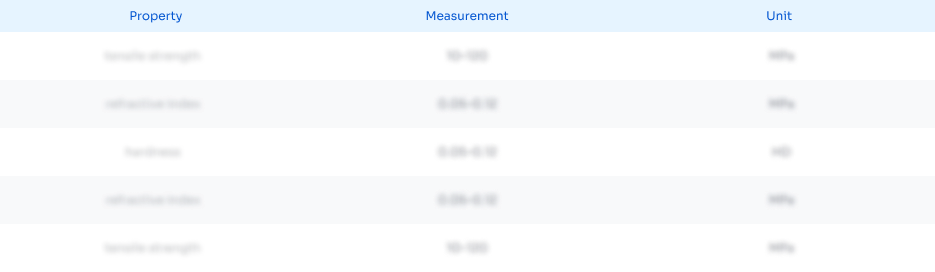
Abstract
Description
Claims
Application Information

- R&D
- Intellectual Property
- Life Sciences
- Materials
- Tech Scout
- Unparalleled Data Quality
- Higher Quality Content
- 60% Fewer Hallucinations
Browse by: Latest US Patents, China's latest patents, Technical Efficacy Thesaurus, Application Domain, Technology Topic, Popular Technical Reports.
© 2025 PatSnap. All rights reserved.Legal|Privacy policy|Modern Slavery Act Transparency Statement|Sitemap|About US| Contact US: help@patsnap.com