Auto-control and auto-detection system for non-decoupled dynamic compaction machine
A technology of automatic detection and dynamic compaction machine, applied in the direction of electrical program control, program control in sequence/logic controller, etc.
- Summary
- Abstract
- Description
- Claims
- Application Information
AI Technical Summary
Problems solved by technology
Method used
Image
Examples
Embodiment Construction
[0021] The present invention is described in detail below in conjunction with accompanying drawing and specific embodiment:
[0022] Such as figure 1 As shown, the automatic control and automatic detection system of the non-decoupling dynamic compaction machine: includes a programmable controller PLC1, a shaft encoder 3, a pressure sensor 4, an electromagnetic reversing valve 5 and a touch screen 2, and the input end of the shaft encoder 3 It is connected to the motor 6 shaft, the input end of the pressure sensor 4 is connected to the motor 6, the input end of the electromagnetic reversing valve 5 is connected to the hydraulic station 7 of the dynamic compaction machine, and the input end of the programmable controller PLC1 is connected to the shaft The output ends of the encoder 3 , the pressure sensor 4 , and the electromagnetic reversing valve 5 are respectively connected, and the output end of the programmable controller PLC1 is connected with the touch screen 2 .
[002...
PUM
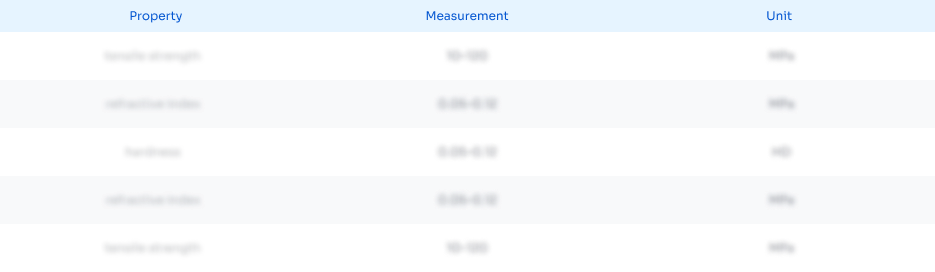
Abstract
Description
Claims
Application Information

- Generate Ideas
- Intellectual Property
- Life Sciences
- Materials
- Tech Scout
- Unparalleled Data Quality
- Higher Quality Content
- 60% Fewer Hallucinations
Browse by: Latest US Patents, China's latest patents, Technical Efficacy Thesaurus, Application Domain, Technology Topic, Popular Technical Reports.
© 2025 PatSnap. All rights reserved.Legal|Privacy policy|Modern Slavery Act Transparency Statement|Sitemap|About US| Contact US: help@patsnap.com