Three-degree-of-freedom ultralow frequency vibration absorber
A shock absorber and ultra-low frequency technology, applied in the direction of non-rotational vibration suppression, etc., can solve the problems of inability to effectively isolate ultra-low frequency vibration, difficulty in achieving ultra-low frequency vibration reduction, increase manufacturing and use, etc., achieve good vibration reduction effect, good Suppression effect, vibration suppression effect
- Summary
- Abstract
- Description
- Claims
- Application Information
AI Technical Summary
Problems solved by technology
Method used
Image
Examples
Embodiment Construction
[0025] The specific embodiments of the present invention will be further described below in conjunction with the accompanying drawings. It should be noted here that the descriptions of these embodiments are used to help understand the present invention, but are not intended to limit the present invention. In addition, the technical features involved in the various embodiments of the present invention described below can be combined with each other as long as they do not constitute a conflict with each other.
[0026] The three-degree-of-freedom ultra-low-frequency shock absorber adopts a parallel structure of positive and negative stiffness in the three-degree-of-freedom directions of space to reduce the natural frequency of the system to achieve the purpose of ultra-low-frequency vibration reduction; among them, positive magnetic stiffness and negative magnetic stiffness are used in the z direction. Stiffness parallel vibration damping mode, and the size of positive and negat...
PUM
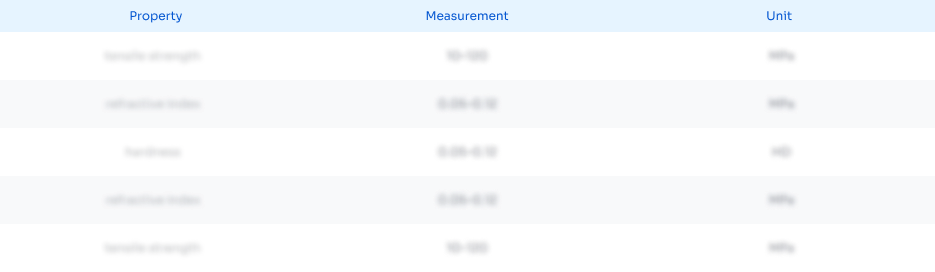
Abstract
Description
Claims
Application Information

- R&D
- Intellectual Property
- Life Sciences
- Materials
- Tech Scout
- Unparalleled Data Quality
- Higher Quality Content
- 60% Fewer Hallucinations
Browse by: Latest US Patents, China's latest patents, Technical Efficacy Thesaurus, Application Domain, Technology Topic, Popular Technical Reports.
© 2025 PatSnap. All rights reserved.Legal|Privacy policy|Modern Slavery Act Transparency Statement|Sitemap|About US| Contact US: help@patsnap.com