Multistage-temperature-control-based fused deposition modeling (FDM) type 3D printing sprayer and temperature control method
A fused filament deposition molding and 3D printing technology, applied in the field of 3D printing, can solve the problems of increasing the burden of the extrusion system, strong fluidity, and slow extrusion speed, so as to avoid nozzle blockage and broken filament, and improve quality.
- Summary
- Abstract
- Description
- Claims
- Application Information
AI Technical Summary
Problems solved by technology
Method used
Image
Examples
Embodiment Construction
[0027] First of all, it should be explained that the present invention relates to control technology, which is an application of computer technology in the field of control. During the implementation of the present invention, the application of multiple software function modules will be involved. The applicant believes that, after carefully reading the application documents and accurately understanding the realization principle and purpose of the present invention, combined with existing known technologies, those skilled in the art can fully implement the present invention by using their software programming skills. The aforementioned software functional modules include but are not limited to: multi-stage temperature control modules for FDM print nozzles, etc., all mentioned in the application documents of the present invention belong to this category, and the applicant will not list them one by one.
[0028] Below in conjunction with accompanying drawing, the specific embodim...
PUM
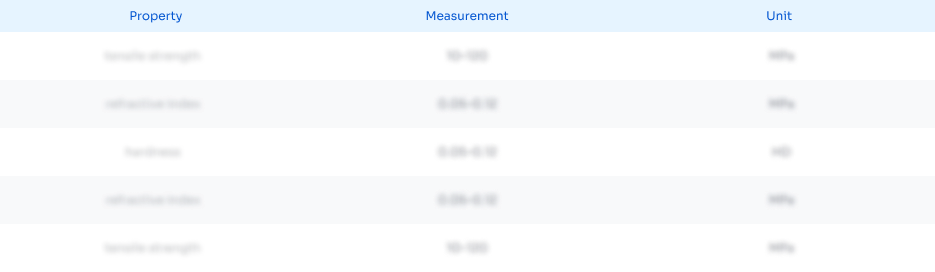
Abstract
Description
Claims
Application Information

- R&D
- Intellectual Property
- Life Sciences
- Materials
- Tech Scout
- Unparalleled Data Quality
- Higher Quality Content
- 60% Fewer Hallucinations
Browse by: Latest US Patents, China's latest patents, Technical Efficacy Thesaurus, Application Domain, Technology Topic, Popular Technical Reports.
© 2025 PatSnap. All rights reserved.Legal|Privacy policy|Modern Slavery Act Transparency Statement|Sitemap|About US| Contact US: help@patsnap.com