Dynamics modeling method of over-constrained heavy parallel machine tool applied to real-time control
A real-time control and over-constraint technology, applied in the direction of digital control, electrical program control, etc., can solve the problems that the elastic dynamic model cannot be applied to the real-time control system and the rigid body dynamic model has low precision, so as to meet the real-time requirements and computational efficiency High, the effect of improving the accuracy of the model
- Summary
- Abstract
- Description
- Claims
- Application Information
AI Technical Summary
Problems solved by technology
Method used
Image
Examples
Embodiment Construction
[0018] The method embodiment of the present invention comprises the following steps as follows:
[0019] 1) According to the structure of the over-constrained heavy-duty parallel machine tool, through the kinematic analysis of the machine tool, the position, velocity and acceleration of each joint of the machine tool are obtained; Establish the velocity relationship between the moving platform of the machine tool and each active joint according to the Jacobian matrix; specifically include:
[0020] 11) Establish a fixed coordinate system O-XY fixed on the machine frame, such as figure 1 As shown, point O is the contact point C between the two columns of the machine tool and the ground 1 、C 3 The midpoint of the center point; the X-axis is horizontally to the right, and the Y-axis is vertically upward; the fixed coordinate system O′-xy established on the moving platform, the center position of the moving platform is recorded as O′, the x-axis is horizontally to the right, and...
PUM
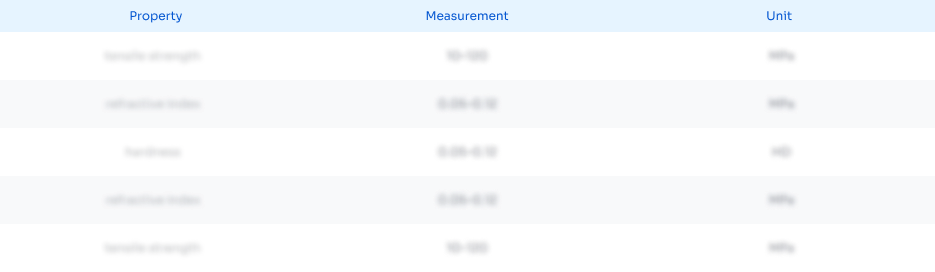
Abstract
Description
Claims
Application Information

- R&D
- Intellectual Property
- Life Sciences
- Materials
- Tech Scout
- Unparalleled Data Quality
- Higher Quality Content
- 60% Fewer Hallucinations
Browse by: Latest US Patents, China's latest patents, Technical Efficacy Thesaurus, Application Domain, Technology Topic, Popular Technical Reports.
© 2025 PatSnap. All rights reserved.Legal|Privacy policy|Modern Slavery Act Transparency Statement|Sitemap|About US| Contact US: help@patsnap.com