Method for eliminating null shift of micro-electromechanical system (MEMS) gyroscope
A gyro and zero-drift technology, which is applied in the field of random walk, temperature drift, and MEMS gyro zero-drift elimination. It can solve the problems of unfavorable single-chip microcomputer and other microprocessor processing and poor real-time adaptability, so as to facilitate processing work, reduce output noise, Overcome the effects of zero drift and temperature drift
- Summary
- Abstract
- Description
- Claims
- Application Information
AI Technical Summary
Problems solved by technology
Method used
Image
Examples
Embodiment Construction
[0030] The present invention will be described in further detail below in conjunction with the accompanying drawings.
[0031] The system principle of the present invention is as figure 1 shown. First of all, the MEMS gyroscope and single-chip microcomputer (MCU) are compactly installed on the circuit board. The AD sampling of the output signal of the gyroscope to the MCU is as short as possible to ensure that the impedance is as small as possible. At the same time, the digital signal and the analog signal are separated to reduce the digital signal to the analog signal. signal interference.
[0032] The noise of the directly sampled gyro output value is relatively large. Taking AD’s ADI646 gyro, pipeline mean filter, and C8051F061 microcontroller as an example, when the frequency band of the ADIXRS646 gyro is set at 400Hz, the noise level is about ±110 (one of 16-bit AD sampling unit, the same below), such as Figure 4 As shown, continuous sampling of 20 values is placed ...
PUM
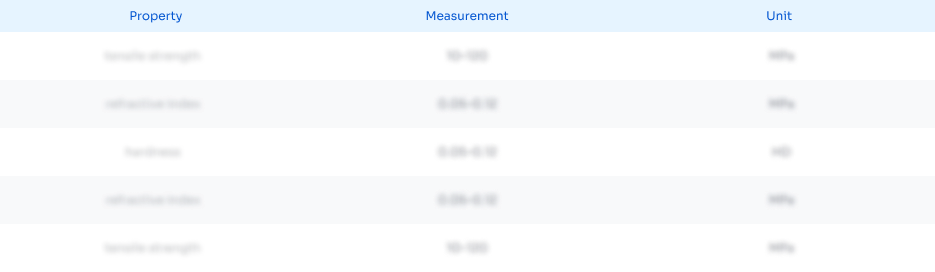
Abstract
Description
Claims
Application Information

- Generate Ideas
- Intellectual Property
- Life Sciences
- Materials
- Tech Scout
- Unparalleled Data Quality
- Higher Quality Content
- 60% Fewer Hallucinations
Browse by: Latest US Patents, China's latest patents, Technical Efficacy Thesaurus, Application Domain, Technology Topic, Popular Technical Reports.
© 2025 PatSnap. All rights reserved.Legal|Privacy policy|Modern Slavery Act Transparency Statement|Sitemap|About US| Contact US: help@patsnap.com