Technological method for reducing belt breaking times in rolling mill starting
A process method and rolling mill technology, applied in the fields of rolling mill control device, metal rolling, manufacturing tools, etc., can solve the problems of affecting the forming rate of the machine, large loss of the forming rate, affecting the production efficiency, etc. The effect of reducing the number of off-line rolls and reducing the strip breakage at the start of the rolling mill
- Summary
- Abstract
- Description
- Claims
- Application Information
AI Technical Summary
Problems solved by technology
Method used
Image
Examples
Embodiment Construction
[0019] Below with reference to the accompanying drawings, through the description of the embodiments, the specific embodiments of the present invention, such as the shape, structure, mutual position and connection relationship between the various parts, the role and working principle of the various parts, etc., will be further described. Detailed instructions:
[0020] as attached figure 1 — attached image 3 Shown, the present invention is a kind of processing method that reduces rolling mill start-up broken band, and rolling mill comprises frame, work roll, control component, and the step of reducing the processing method of rolling mill start-up broken band is:
[0021] (1) Before the shutdown of the rolling mill, increase the target thickness set at the strip outlet by 30%-40%;
[0022] (2) After increasing the target thickness value, reduce the positive roll bending force exerted by each stand on the work roll;
[0023] (3) Modify the target thickness, and the rolling ...
PUM
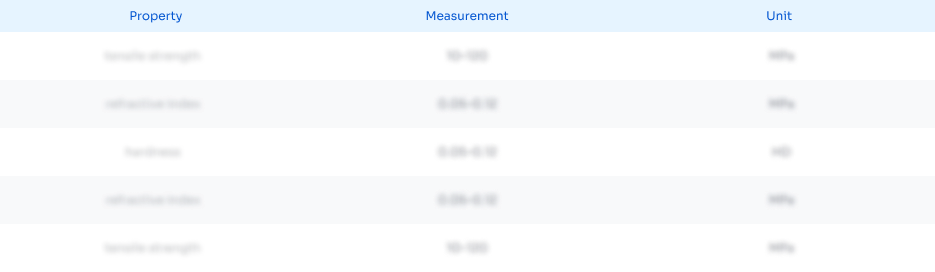
Abstract
Description
Claims
Application Information

- R&D
- Intellectual Property
- Life Sciences
- Materials
- Tech Scout
- Unparalleled Data Quality
- Higher Quality Content
- 60% Fewer Hallucinations
Browse by: Latest US Patents, China's latest patents, Technical Efficacy Thesaurus, Application Domain, Technology Topic, Popular Technical Reports.
© 2025 PatSnap. All rights reserved.Legal|Privacy policy|Modern Slavery Act Transparency Statement|Sitemap|About US| Contact US: help@patsnap.com