Space 5 freedom degree parallel robot mechanism
A degree of freedom, robot technology, applied in manipulators, program-controlled manipulators, manufacturing tools, etc., can solve the problems of repair, platform prosthesis fixation, heavy body and other problems, and achieve the effect of low manufacturing cost, few mechanism joints, and simple structure
- Summary
- Abstract
- Description
- Claims
- Application Information
AI Technical Summary
Problems solved by technology
Method used
Image
Examples
Embodiment 1
[0020] As shown in the attached figure, the 5-DOF parallel robot mechanism in this space consists of the lower platform (VI), the upper platform (VII), five branch chains (Ⅰ, Ⅱ, Ⅲ, Ⅳ, Ⅴ) connecting the above two platforms, and the terminal execution. Device (Ⅷ) composition. It is characterized in that: the lower platform (Ⅵ) and the upper platform (Ⅶ) are circular; the five branch chains are evenly distributed along the circumferential direction and have the same length; The other four branches of the same type (Ⅱ, Ⅲ, Ⅳ, Ⅴ) have the same configuration; each branch includes three connected kinematic pairs and a driving motor (3); the end effector (Ⅷ) and Connected to the upper platform (Ⅶ).
Embodiment 2
[0022] see figure 1 , figure 2 with image 3 , this embodiment is basically the same as Embodiment 1, and the special features are as follows
[0023] The special-shaped branch chain (I) consists of a cross universal pair (1), a motor base (2), a driving motor (3), a motor fixing plate (4), and a moving pair (6) from bottom to top It is combined with a cross universal pair (Ⅰ-8), and the other four branches of the same type (II, III, IV, Ⅴ) with the same configuration are composed of a cross universal pair (1) and a motor from bottom to top. seat (2), a driving motor (3), a motor fixing plate (4), a moving pair (6) and a ball pair (Ⅱ-8); the 5 branch chain lower connecting rods (5) are ball wires rod, the upper connecting rod (7) is screwed to the lower connecting rod (5) to form a moving pair (6); the moving pair (6) is a driving pair, and the lower end of the lower connecting rod (5) is connected to the drive motor (3) The output shaft and the five moving pairs (6) have...
PUM
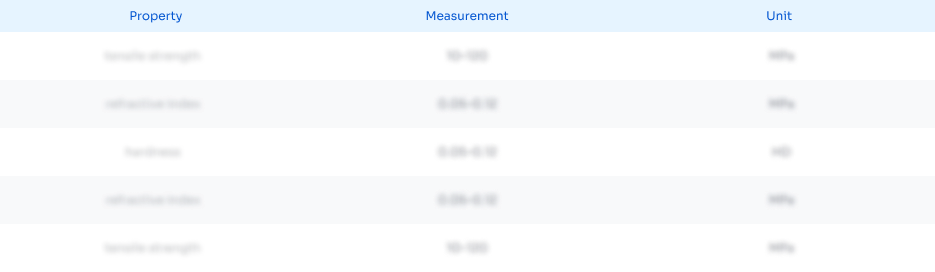
Abstract
Description
Claims
Application Information

- R&D
- Intellectual Property
- Life Sciences
- Materials
- Tech Scout
- Unparalleled Data Quality
- Higher Quality Content
- 60% Fewer Hallucinations
Browse by: Latest US Patents, China's latest patents, Technical Efficacy Thesaurus, Application Domain, Technology Topic, Popular Technical Reports.
© 2025 PatSnap. All rights reserved.Legal|Privacy policy|Modern Slavery Act Transparency Statement|Sitemap|About US| Contact US: help@patsnap.com