Angle sensor
An angle sensor, sensor technology, applied in the direction of converting sensor output, instruments, measuring devices, etc., can solve the problems of uneven magnetic flux density of helical coils, magnetic flux leakage, resolver output error, etc., to improve detection accuracy and performance, The effect of homogenizing the magnetic flux density
- Summary
- Abstract
- Description
- Claims
- Application Information
AI Technical Summary
Problems solved by technology
Method used
Image
Examples
no. 1 Embodiment approach
[0051] Hereinafter, a first embodiment embodying the angle sensor of the present invention will be described in detail with reference to the drawings.
[0052] figure 1 It is a sectional view showing a part of the motor 70 to which the angle sensor 9 of this embodiment is mounted. The motor 70 includes: a motor case 71; a case cover 72 for covering the opening of the motor case 71; a motor stator 73 fixed to the motor case 71; a motor rotor 74 provided inside the motor stator 73; A motor shaft 75 integrally provided at the center of the motor rotor 74; a pair of bearings 76, 77 for rotatably supporting the motor shaft 75 between the motor housing 71 and the housing cover 72.
[0053] The motor housing 71 and the housing cover 72 are formed by casting aluminum alloy or the like. The motor stator 73 has a coil 78 and is fixed to the inner periphery of the motor housing 71 . The motor stator 73 is excited by energizing the coil 78 to generate magnetic force.
[0054] The moto...
no. 2 Embodiment approach
[0110] Next, a second embodiment of an angle sensor of the present invention will be described in detail with reference to the drawings.
[0111] Figure 23 is a front cross-sectional view showing the angle sensor 301 and the motor 302 provided with the angle sensor 301 according to this embodiment (hereinafter, for convenience, figure 1 orientation as the front view). The motor 302 includes: a motor housing 311 having a substantially disc-shaped appearance; a rotating shaft 314 covered by the motor housing 311 and rotatably supported at the inner center of the motor housing 311 via bearings 312, 313; a motor rotor 315, It is fixed on the outer circumference of the rotating shaft 314 inside the motor housing 311 ; the motor stator 316 is fixed on the inner side of the motor housing 311 through a gap on the outer circumference side of the motor rotor 315 . A coil 317 is provided on the motor stator 316 .
[0112] exist Figure 23 Among them, a housing portion 311 a for hous...
no. 3 Embodiment approach
[0129] Next, a third embodiment of the angle sensor of the present invention will be described in detail with reference to the drawings.
[0130] Figure 29 is part of the representation of the angle sensor based on Figure 27 enlarged sectional view of the . This embodiment differs from the second embodiment in the arrangement of the annular facing portions 323c and 335a. That is, in the rotor-side ring-shaped metal member 323 , the ring-shaped opposing portion 323 c is disposed on the outer peripheral portion of the metal member 323 . Further, a groove 323d in which the resolver coil 341 is arranged is formed on the side of the annular facing portion 323c close to one side surface in the axial direction (the surface 321a of the rotor substrate 321). On the other hand, in the stator-side ring-shaped metal member 335 , the ring-shaped facing portion 335 a is disposed at a position facing the ring-shaped facing portion 323 c of the rotor-side ring-shaped metal member 323 . ...
PUM
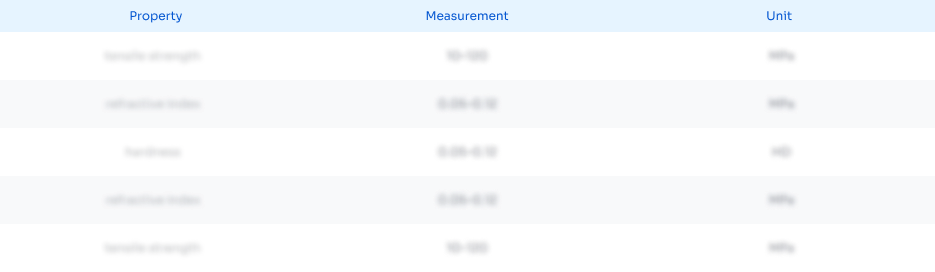
Abstract
Description
Claims
Application Information

- R&D
- Intellectual Property
- Life Sciences
- Materials
- Tech Scout
- Unparalleled Data Quality
- Higher Quality Content
- 60% Fewer Hallucinations
Browse by: Latest US Patents, China's latest patents, Technical Efficacy Thesaurus, Application Domain, Technology Topic, Popular Technical Reports.
© 2025 PatSnap. All rights reserved.Legal|Privacy policy|Modern Slavery Act Transparency Statement|Sitemap|About US| Contact US: help@patsnap.com