Assembly process for built-in heat exchanger of solar split water tank
An assembly process and heat exchanger technology, applied in auxiliary devices, manufacturing tools, metal processing equipment, etc., can solve the problems of low assembly efficiency and high labor intensity, and achieve the effect of high assembly efficiency and reduced labor intensity
- Summary
- Abstract
- Description
- Claims
- Application Information
AI Technical Summary
Problems solved by technology
Method used
Image
Examples
Embodiment Construction
[0016] The present invention will be further described below in conjunction with accompanying drawing:
[0017] An assembly process of a solar split water tank built-in heat exchanger, the assembly process is as follows:
[0018] 1) Place the solar heat exchanger 5 on the heat exchanger bracket 4 and fix it with a positioning device;
[0019] 2) Move the inner tank cylinder 6 to the cylinder bracket 7, the opening of the inner tank cylinder 6 faces the direction of the solar heat exchanger 5, refer to the attached image 3 ;
[0020] 3) Move the inner tank cylinder 6 left and right along the cylinder bracket 7 until the heat exchanger joint 11 is aligned with the inner tank cylinder tube seat 13;
[0021] 4) Use the positioning guide pin 12 to pass through the tube seat 13 of the inner tank cylinder and insert it into the heat exchanger joint 11, so that the heat exchanger joint 11 can be smoothly connected with the tube base 13 of the inner tank tube. Figure ...
PUM
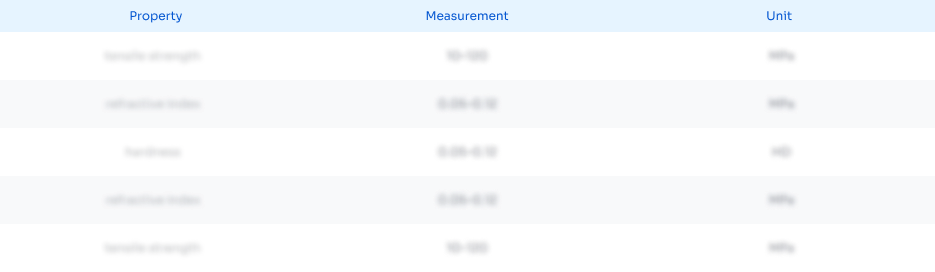
Abstract
Description
Claims
Application Information

- R&D
- Intellectual Property
- Life Sciences
- Materials
- Tech Scout
- Unparalleled Data Quality
- Higher Quality Content
- 60% Fewer Hallucinations
Browse by: Latest US Patents, China's latest patents, Technical Efficacy Thesaurus, Application Domain, Technology Topic, Popular Technical Reports.
© 2025 PatSnap. All rights reserved.Legal|Privacy policy|Modern Slavery Act Transparency Statement|Sitemap|About US| Contact US: help@patsnap.com