Integrally-assembled concrete structural system adopting steel bar lapping mode
A concrete structure and monolithic technology, which is applied in the direction of building structure and construction, can solve the problems of high sleeve processing and manufacturing costs, increase construction cost, and difficulty in component production, so as to simplify manufacturing difficulty, save construction cost, and speed up construction speed effect
- Summary
- Abstract
- Description
- Claims
- Application Information
AI Technical Summary
Problems solved by technology
Method used
Image
Examples
Embodiment Construction
[0025] The present invention will be described in detail below in conjunction with examples.
[0026] The invention adopts the design, component manufacturing and construction method of the assembled integral concrete structure in the lap joint connection mode, and produces a new connection mode between prefabricated components. In the design, it is calculated and designed according to the ordinary cast-in-place reinforced concrete, and the effective overlap degree between the components is reserved during the fabrication and processing of the components. In the construction project of the assembly site, after the prefabricated components are installed in place, the ordinary concrete pouring required by the design is used. That is, there is no need to use additional sleeves and spiral bars, and there is no need for accurate alignment of the steel bars between the components and the reserved holes. On the premise of ensuring structural safety, the difficulty of component process...
PUM
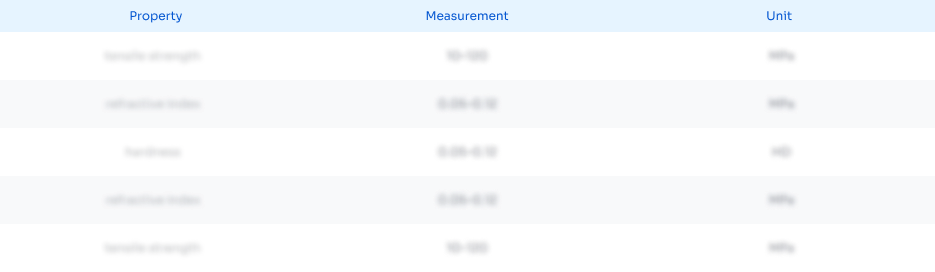
Abstract
Description
Claims
Application Information

- Generate Ideas
- Intellectual Property
- Life Sciences
- Materials
- Tech Scout
- Unparalleled Data Quality
- Higher Quality Content
- 60% Fewer Hallucinations
Browse by: Latest US Patents, China's latest patents, Technical Efficacy Thesaurus, Application Domain, Technology Topic, Popular Technical Reports.
© 2025 PatSnap. All rights reserved.Legal|Privacy policy|Modern Slavery Act Transparency Statement|Sitemap|About US| Contact US: help@patsnap.com