Self-adaption control method of shear edge position of crank shaft flywheel shear in cold-rolling continuous processing line
An adaptive control and processing line technology, applied in rolling mill control devices, metal rolling, metal rolling, etc., can solve problems such as insufficient glycerin lubrication of crankshaft bearings, inability to adapt to the power-on time of pneumatic solenoid valves, abnormal shutdown of production lines, etc. , to achieve the effect of reducing the failure rate of abnormal parking, reducing the workload of maintenance and debugging, and ensuring the continuity of operation
- Summary
- Abstract
- Description
- Claims
- Application Information
AI Technical Summary
Problems solved by technology
Method used
Image
Examples
Embodiment Construction
[0022] The present invention will be further described below in conjunction with the embodiments and accompanying drawings.
[0023] The self-adaptive control of the position of the crankshaft flywheel shears in the cold rolling continuous processing line includes the following steps: installing an absolute encoder on the crankshaft bearing of the crankshaft flywheel shears; , take a point on the crankshaft rotating surface as a fixed point, and determine the angle information of the fixed point during initialization; record the accumulated pulse number of the absolute encoder when each shearing is completed, and calculate the angle information of the fixed point on the current crankshaft rotating surface; compare The angle information of the fixed point at the completion of each shearing and the angle information of the fixed point at the time of initialization adjust the parameter of the power-on time of the pneumatic solenoid valve to control the clutch engagement time and b...
PUM
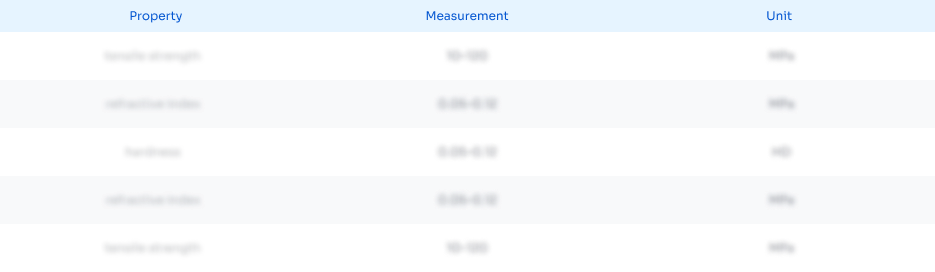
Abstract
Description
Claims
Application Information

- R&D Engineer
- R&D Manager
- IP Professional
- Industry Leading Data Capabilities
- Powerful AI technology
- Patent DNA Extraction
Browse by: Latest US Patents, China's latest patents, Technical Efficacy Thesaurus, Application Domain, Technology Topic, Popular Technical Reports.
© 2024 PatSnap. All rights reserved.Legal|Privacy policy|Modern Slavery Act Transparency Statement|Sitemap|About US| Contact US: help@patsnap.com