Model correcting method based on defective modal structure
A defect modal and structural model technology, applied in special data processing applications, instruments, electrical digital data processing, etc., can solve the problem that no one has proposed, does not consider the information of measurement eigenvectors, and cannot guarantee positive definiteness or semi-positive definiteness, etc. problems, to avoid errors and improve accuracy
- Summary
- Abstract
- Description
- Claims
- Application Information
AI Technical Summary
Problems solved by technology
Method used
Image
Examples
Embodiment Construction
[0018] combine figure 1 , a structural model correction method based on defect modes, the steps are as follows:
[0019] Step 1. Format the initial data, that is, separate the measured degrees of freedom from the unmeasured degrees of freedom in the modal data by adjusting the number of degrees of freedom, and convert the complex modal data to real numbers, so as to ensure that all operations are carried out in real time. execute in form; combine figure 2 , the specific steps to format the initial data are:
[0020] Step 1-1. Set all degrees of freedom as {1, 2, ... N}, {m 1 , m 2 ,...m l} are l measured degrees of freedom, and the remaining unmeasured degrees of freedom are denoted as {m l+1 ,...m N};
[0021] Step 1-2, separate the measured degrees of freedom from the unmeasured degrees of freedom to obtain the permutation matrix P(m 1 , m 2 ,...m l , m l+1 ,...m N ), where P(m 1 , m 2 ,...m l , m 1+1 ,...m N ) by all column vectors of the N-order identity ...
PUM
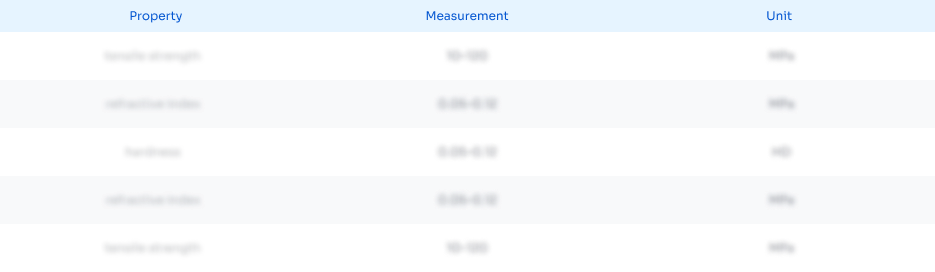
Abstract
Description
Claims
Application Information

- R&D
- Intellectual Property
- Life Sciences
- Materials
- Tech Scout
- Unparalleled Data Quality
- Higher Quality Content
- 60% Fewer Hallucinations
Browse by: Latest US Patents, China's latest patents, Technical Efficacy Thesaurus, Application Domain, Technology Topic, Popular Technical Reports.
© 2025 PatSnap. All rights reserved.Legal|Privacy policy|Modern Slavery Act Transparency Statement|Sitemap|About US| Contact US: help@patsnap.com