Dynamic and static testing system and method for multifunctional wharf structure
A static test, multi-functional technology, used in the testing of machine/structural components, the use of applied stable tension/pressure to test the strength of materials, the testing of mechanical components, etc. The effect of convenience, stable structure and strong versatility
- Summary
- Abstract
- Description
- Claims
- Application Information
AI Technical Summary
Problems solved by technology
Method used
Image
Examples
Embodiment Construction
[0036] The preferred embodiments of the present invention will be described in detail below in conjunction with the accompanying drawings; it should be understood that the preferred embodiments are only for illustrating the present invention, rather than limiting the protection scope of the present invention.
[0037]Fig. 1 is the front view of the high-pile frame wharf structure test loading provided by the embodiment of the present invention, Fig. 2 is the side view of the high-pile frame wharf structure test loading provided by the embodiment of the present invention, and Fig. 3 is the high-pile frame provided by the embodiment of the present invention The loading top view of the wharf structure test, Fig. 4 is a flow chart of the wharf structure dynamic test method provided by the embodiment of the present invention, Fig. 5 is a principle block diagram of the wharf structure dynamic test device provided by the embodiment of the present invention, as shown in the figure, mult...
PUM
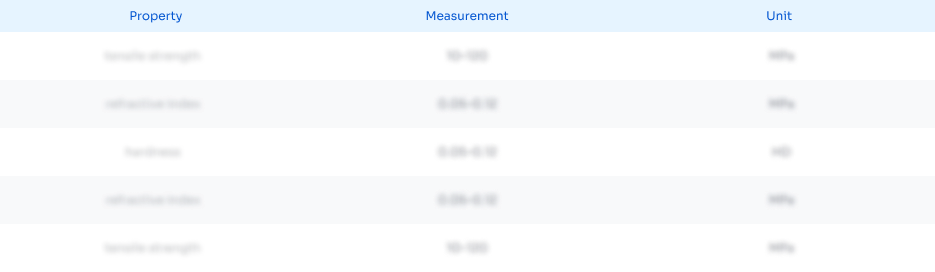
Abstract
Description
Claims
Application Information

- R&D
- Intellectual Property
- Life Sciences
- Materials
- Tech Scout
- Unparalleled Data Quality
- Higher Quality Content
- 60% Fewer Hallucinations
Browse by: Latest US Patents, China's latest patents, Technical Efficacy Thesaurus, Application Domain, Technology Topic, Popular Technical Reports.
© 2025 PatSnap. All rights reserved.Legal|Privacy policy|Modern Slavery Act Transparency Statement|Sitemap|About US| Contact US: help@patsnap.com