Wheel groove broach layered multi-tool tooth groove rough/finish-milling method
A technology of wheel groove broaching and rough milling, which is applied in the field of tooth groove milling, which can solve the problems of low processing efficiency, high cutting heat, and easy stress generation, so as to reduce tool production costs, reduce the value of tooth groove roughness, and reduce friction and squeeze effect
- Summary
- Abstract
- Description
- Claims
- Application Information
AI Technical Summary
Problems solved by technology
Method used
Image
Examples
Embodiment Construction
[0019] Such as figure 2 As shown, a method of layered multi-knife rough and fine milling of tooth grooves by a wheel groove broach of the present invention comprises a processing step of rough milling of tooth grooves by a wheel groove broach and a processing step of fine milling of tooth grooves. The cutter performs rough and fine milling of tooth grooves. The tooth groove depth of the processed wheel groove broach is 21mm. The rough milling process selects a suitable common and commonly used single-angle cogging milling cutter, and divides into four rough milling procedures.
[0020] Such as image 3 As shown, the rough milling program of the first layer is divided into three cutters. During rough milling, the depth of the milling groove is about 1 / 4 of the total depth, and the first cut is slotted in the middle of the tooth groove to provide sufficient chip space for milling the second and third cuts. Carry out the second and third rough milling at the tooth back 2 and...
PUM
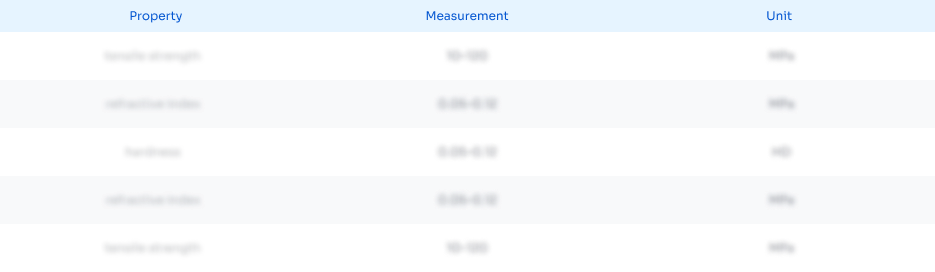
Abstract
Description
Claims
Application Information

- R&D
- Intellectual Property
- Life Sciences
- Materials
- Tech Scout
- Unparalleled Data Quality
- Higher Quality Content
- 60% Fewer Hallucinations
Browse by: Latest US Patents, China's latest patents, Technical Efficacy Thesaurus, Application Domain, Technology Topic, Popular Technical Reports.
© 2025 PatSnap. All rights reserved.Legal|Privacy policy|Modern Slavery Act Transparency Statement|Sitemap|About US| Contact US: help@patsnap.com