Cage-shaped rotor magnetic coupling capable of regulating speed
A magnetic coupling and cage rotor technology, applied in the direction of asynchronous induction clutch/brake, etc., can solve the problems of unsuitable for high-power electromechanical equipment transmission, poor reliability, long design cycle, etc., to facilitate serial design and manufacture , Reduce design and production costs, simple processing and assembly
- Summary
- Abstract
- Description
- Claims
- Application Information
AI Technical Summary
Problems solved by technology
Method used
Image
Examples
Embodiment Construction
[0041] The present invention will be described in further detail below in conjunction with the accompanying drawings. Such as Figure 1-13 As shown, an adjustable speed cage rotor magnetic coupler includes a power input shaft 1, a coupling device, a permanent magnet outer rotor assembly, a cage inner rotor assembly, a power output shaft 22 and a mechanical speed regulating device; The permanent magnet outer rotor assembly is set on the outside of the cage-type inner rotor assembly, and there is a uniform air gap between the two; the permanent magnet outer rotor assembly is connected with the power input shaft 1 through a connecting device, and the cage The inner rotor assembly is connected to the load through the power output shaft 22, and the mechanical speed regulating device is installed on the outside of the right casing 7, which can drive the connecting device and the permanent magnet outer rotor assembly to move axially;
[0042] The power input shaft 1 is a stepped sha...
PUM
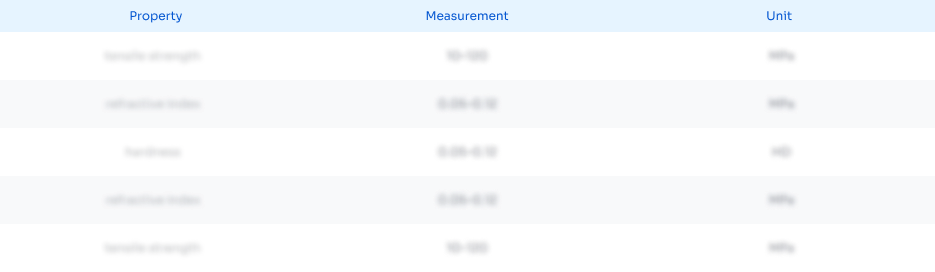
Abstract
Description
Claims
Application Information

- R&D
- Intellectual Property
- Life Sciences
- Materials
- Tech Scout
- Unparalleled Data Quality
- Higher Quality Content
- 60% Fewer Hallucinations
Browse by: Latest US Patents, China's latest patents, Technical Efficacy Thesaurus, Application Domain, Technology Topic, Popular Technical Reports.
© 2025 PatSnap. All rights reserved.Legal|Privacy policy|Modern Slavery Act Transparency Statement|Sitemap|About US| Contact US: help@patsnap.com